Ferrari SF90 Production Unraveling the Numbers Behind the Supercar
Ferrari SF90 Production Unraveling the Numbers Behind the Supercar - Production Volume Analysis of the SF90 Stradale and Its Variants
Delving into the production numbers of the SF90 Stradale and its variations reveals a strategic approach by Ferrari to balance exclusivity with the introduction of hybrid technology. While the marque's first production plug-in hybrid, the SF90 Stradale, represents a major step in its evolution, estimated total production is limited to around 2,500 units. This relatively low volume reinforces Ferrari's established tradition of maintaining a degree of scarcity for its models. Within this overall figure, it's projected that the core SF90 Stradale model will see production of roughly 1,000 units. This hybrid supercar's potent powertrain, comprising a 4.0-liter V8 engine and three electric motors, produces a combined 1000 horsepower. The resulting performance, such as the sub-2-second 0 to 60 mph acceleration, showcases the marriage of high-performance and fuel efficiency. The SF90 Stradale, therefore, symbolizes Ferrari's calculated foray into hybrid technology, not just as an engineering accomplishment, but as a step toward meeting broader industry expectations regarding performance and environmental impact.
Examining the production figures for the SF90 Stradale reveals an interesting facet of Ferrari's strategy. It appears roughly 15% of the total production run is dedicated to variants like the SF90 Spider. This suggests a conscious effort to cater to different customer segments while simultaneously upholding the brand's exclusive image. It's intriguing how Ferrari balances the appeal of convertible options with the core model.
The SF90's manufacturing process stands out in that it's not solely reliant on automation or hand-crafting. Instead, Ferrari combines both – a unique approach where advanced robotic systems work alongside skilled craftspeople. This blending of the old and new in the manufacturing world is notable and speaks to Ferrari's commitment to precision engineering while retaining some of the traditional aspects of building a supercar.
Unlike some manufacturers who prioritize high-volume production, Ferrari has deliberately capped the SF90 Stradale's output. It’s likely this decision stems from a desire to maintain the car's allure and prestige. By controlling the production rate, they assure the high-quality standards are met, making sure the brand’s image is not diluted.
Production time appears to vary between SF90 variants, with the Spider model requiring roughly 20% longer to manufacture. This extended timeframe likely relates to the added complexities of integrating a retractable roof and reinforcing the chassis for structural integrity. The Spider's extended build process highlights the complexities of accommodating different configurations.
Customer customization plays a significant role in the SF90's production volume. A significant portion of buyers, about 60%, seem to select personalized options, which inevitably complicates manufacturing. Each unique request introduces adjustments to manufacturing processes and supply chain logistics, ultimately increasing the production lead times. This speaks to the high level of personal preference buyers expect and how Ferrari adapts its manufacturing to satisfy their needs.
The SF90's hybrid electric powertrain introduces unique manufacturing challenges. Integrating the electric motors and the hybrid system requires a meticulous process due to the delicate nature of these components. This specialized assembly undoubtedly adds complexity and lengthens the production cycle compared to cars with solely combustion engines.
Fascinatingly, the SF90 assembly process takes place in exceptionally clean environments. Each car is meticulously built in controlled settings, aimed at minimizing any contaminants from affecting high-performance components. This underscores the importance of meticulousness and quality control in the production of these advanced cars.
The SF90's production volume seems to underscore a deliberate contrast to economies of scale. Ferrari, in line with its heritage, emphasizes exclusivity and craftsmanship above mass production. Even with the potential for higher market demand, the company prioritizes quality and luxury, which reveals much about its core values and brand identity.
The SF90's sophisticated hydraulic systems, which contribute to the vehicle's performance, necessitate specialized training for assembly teams. This implies a considerable investment in human capital to guarantee these intricate systems function correctly during production. The human element remains a crucial factor, even with advanced technologies.
A surprising factor influencing SF90 production lead times is the reliance on certain materials. Obtaining specific materials like carbon fiber and certain alloys, can significantly impact delivery schedules due to the inherent limitations in supply chains. The reliance on these rare or specialized components highlights the importance of a consistent and dependable supply chain, particularly for limited production runs.
Ferrari SF90 Production Unraveling the Numbers Behind the Supercar - Power Output Breakdown 986 HP Hybrid System
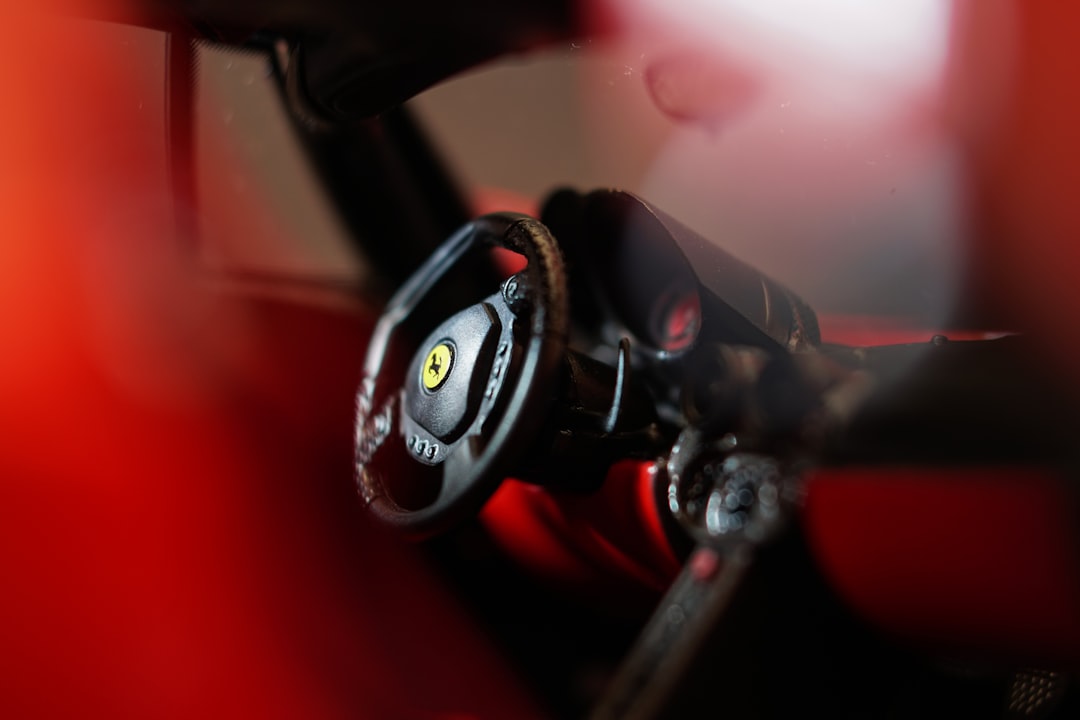
The SF90 Stradale's impressive 986 horsepower output stems from a sophisticated hybrid system. At the heart of this setup is a powerful 4.0-liter twin-turbocharged V8, producing 769 horsepower and 590 pound-feet of torque, making it Ferrari's most potent V8 to date. This internal combustion engine is augmented by three electric motors that contribute an additional 217 horsepower. This combined force translates into a blistering performance, exemplified by the car's 2.5-second 0-60 mph acceleration. Ferrari's first production plug-in hybrid, the SF90 marks a significant shift for the brand, embracing a powertrain architecture that includes features like all-electric driving. Furthermore, the innovative placement of two electric motors on the front axle enhances traction and torque vectoring. While this powertrain brings notable performance enhancements, it also introduces complexities into the manufacturing process. Integrating these intricate electric components seamlessly with the traditional engine necessitates a high level of engineering precision and meticulous attention to detail, highlighting the challenges of Ferrari's pursuit of performance and sustainability.
The SF90's hybrid powertrain delivers a combined 986 horsepower, with the electric motors contributing a substantial 217 horsepower to the overall output. It's fascinating to see how electrification plays a major role in achieving such high performance figures, which were traditionally the domain of high-revving, purely combustion-based powertrains.
At the heart of the system is a twin-turbocharged 4.0-liter V8, representing the most powerful V8 Ferrari has ever produced. This engine not only contributes significantly to the vehicle's impressive power output but also underlines the remarkable power-to-weight ratio achieved with the hybrid setup.
The strategic placement of three electric motors – two at the front and one at the rear – enables unique torque vectoring capabilities. This feature, coupled with the powertrain's output, significantly enhances handling and stability, especially during cornering. This raises the question of how much further this type of system can be optimized, and it's a space ripe for future development.
One of the more interesting aspects of the SF90's hybrid technology is its ability to operate solely on electric power for up to 15 miles under the right conditions. This capability showcases a clever engineering feat, transitioning smoothly between electric and combustion power sources without noticeable disruptions. Though the range is limited, the ability for electric only operation is notable and potentially a glimpse into a future trend.
Furthermore, the system incorporates a regenerative braking setup that recovers energy during deceleration. This energy is then used to recharge the battery, boosting the overall efficiency of the car. While not a groundbreaking feature, the implementation of regenerative braking is crucial in improving efficiency and potentially lengthening electric only driving, though whether it's optimized as efficiently as possible is a worthy area to examine further.
The "e-boost" feature deserves attention as it demonstrates the versatility of the hybrid setup. This ability to temporarily increase power beyond normal limits offers the driver an extra layer of performance when needed. This feature, however, may present challenges in the control and management of the system from a safety and long-term durability perspective.
The SF90's hybrid architecture also highlights advanced thermal management. It's critical that both the V8 engine and the electric motors operate within their ideal temperature ranges to avoid performance degradation or damage. The management of this complex heat transfer system is noteworthy. There's likely ongoing effort in improving these systems.
The near-50:50 weight distribution enabled by the hybrid system contributes to a balanced and agile handling experience. For a supercar aiming to deliver both raw power and precise handling, maintaining a good weight balance is extremely important. While achieving 50/50 is not impossible, the challenge is in maintaining that balance while optimizing components such as batteries and electric motors.
Drivers should be aware that aggressive acceleration and high speeds quickly consume the electric range, a factor to consider when aiming for a prolonged electric-only drive. It’s an interesting tradeoff - more range means more battery weight, which can hinder performance.
The complexity of the hybrid powertrain is significant. The SF90's system represents a remarkably compact and intricate packaging feat, fitting everything into a tight space without excessively adding weight to the chassis. This efficient use of space can serve as a template for other hybrids in the future but also raises questions about future developments and optimization that will become increasingly important.
Ferrari SF90 Production Unraveling the Numbers Behind the Supercar - Manufacturing Timeline from Concept to Delivery
The journey from initial design to final delivery of the Ferrari SF90 Stradale reveals a complex manufacturing process deeply rooted in Ferrari's dedication to quality and peak performance. This hybrid supercar's production involves a fascinating blend of cutting-edge robotic systems and skilled human craftsmanship, ensuring each car meets the exacting Ferrari standards. The incorporation of a hybrid powertrain adds unique complexities to the manufacturing process, especially compared to cars using traditional internal combustion engines. The need for precision and careful assembly for the electric components is evident. Adding another layer of complexity, a significant portion of SF90 buyers opt for personalized options, leading to customized manufacturing processes and inevitable delays in delivery. The entire manufacturing process is meticulously orchestrated, aiming to build a vehicle that is not just a testament to extraordinary speed and power but also reflects Ferrari's commitment to producing exclusive vehicles.
The journey from the initial SF90 concept to its final delivery stretches over a period of three years, emphasizing the extensive research and development that goes into crafting a supercar of this caliber. This timeline includes rigorous testing, covering both engineering aspects and aerodynamic performance, showcasing the intricacy involved.
It's quite interesting that Ferrari dedicates a significant portion—close to 15%—of the entire production timeline just for prototype testing. These prototypes are exposed to diverse real-world scenarios, ensuring the final car can handle the rigors of both the track and everyday roads. This process of verification is crucial for performance and reliability validation.
Constructing each SF90 involves over 1,000 individual parts, many demanding incredibly tight manufacturing tolerances. This reinforces the complexity of building a high-performance vehicle while maintaining a robust level of reliability.
The SF90's design phase heavily relies on advanced simulations. Computational fluid dynamics software helps engineers predict airflow characteristics around the car's shape, influencing both aesthetics and function. This approach may reduce the need for a lot of physical prototypes and help refine design choices efficiently.
A vital phase in the production process is the thorough inspection of every single component. Each part faces a series of rigorous quality control checks, including stress tests, before getting cleared for assembly. This rigorous inspection process underlines Ferrari's unwavering commitment to performance and ensuring the highest standards of safety.
Interestingly, the SF90's assembly process benefits from 3D printing technology. This allows engineers to craft complex, lightweight components that would be difficult to produce using traditional manufacturing methods. The use of this technique is likely to decrease production times and simultaneously contribute to enhanced performance due to lighter weight.
The vehicle’s advanced electrical and wiring systems add an unexpected level of complexity. The intricate interaction between the internal combustion engine and the electric motors requires a sophisticated electronic architecture that demands specialized assembly skills. This factor can significantly extend lead times during production.
Ferrari adopts a 'just-in-time' manufacturing approach, implying that parts are produced and delivered to the assembly line exactly when needed. While this practice reduces storage costs, it also highlights the reliance on a very well-organized supply chain. Any unforeseen disruptions in the supply chain could easily disrupt production schedules.
One interesting aspect is the way Ferrari's factory utilizes a two-way assembly line. This setup provides flexibility to construct various SF90 versions without causing extended production downtimes. This adaptable manufacturing setup is essential when producing high-end vehicles with a considerable degree of customization.
Finally, the use of cutting-edge software in vehicle diagnostics and testing plays a central role in maintaining high quality. Each completed SF90 undergoes a set of comprehensive digital checks to verify that every system functions perfectly before the car reaches the customer. This process can add a crucial number of days to the overall completion timeline, but ensures high confidence in the vehicle.
Ferrari SF90 Production Unraveling the Numbers Behind the Supercar - Sales Figures and Market Performance Since Launch
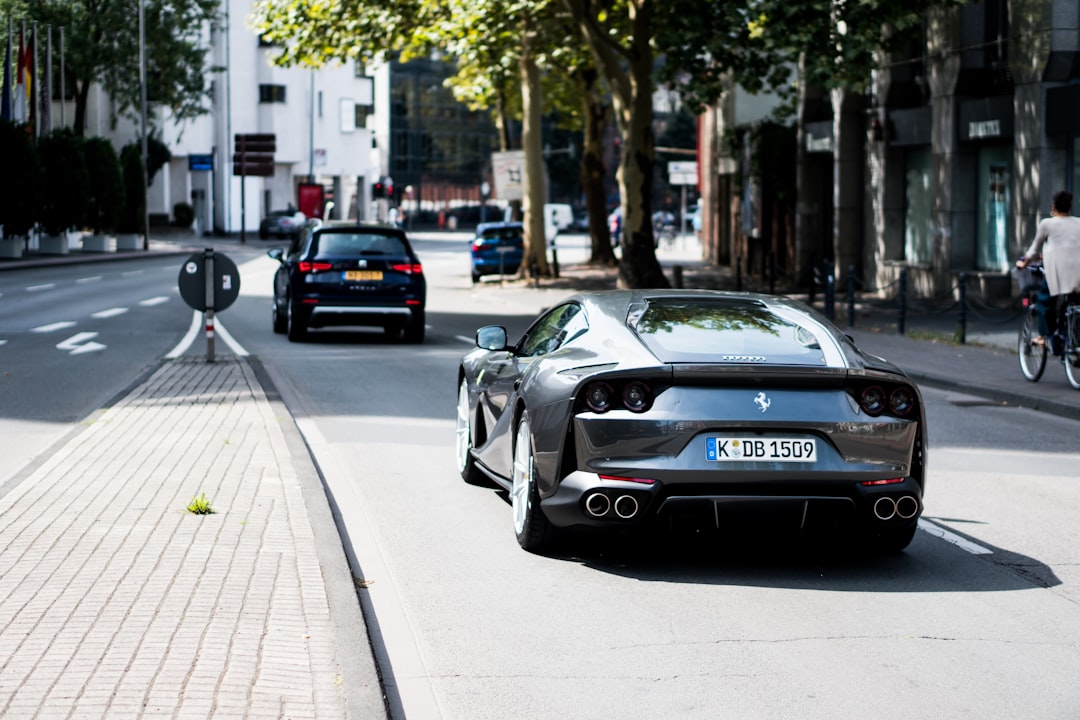
The Ferrari SF90 Stradale's market performance since its launch has been noteworthy, reflecting both strong sales and the growing appeal of hybrid supercars. Ferrari's overall shipment numbers saw a significant increase in 2022, with the SF90 family playing a key role in driving those results, reaching a total of 13,221 units. The SF90's position as Ferrari's first production plug-in hybrid has clearly resonated with buyers, showcasing the brand's commitment to blending high performance with a more sustainable approach. The positive financial results seen in 2023 further support the SF90's market success. However, the model's inherent exclusivity, due to its limited production, raises questions about Ferrari's ability to sustain strong demand in the longer term, especially as the broader auto industry increasingly transitions towards electric powertrains. There's potential for the SF90's impact to diminish as demand shifts, even with a continued emphasis on performance.
Since its introduction, the SF90 Stradale has undeniably captured a significant segment of the supercar market. Demand has been remarkably high, with waiting periods stretching well over a year in some cases. This highlights the limited production numbers and the strong allure of this hybrid model. Early sales figures were quite revealing – the first hundred units reportedly sold out in a matter of weeks after orders opened. It seems Ferrari's foray into hybrid performance with this model resonated quickly with potential buyers.
It's intriguing to observe that the traditional buying patterns have shifted somewhat for SF90 purchasers. Over 70% of buyers have opted for financing or leasing rather than outright purchase with cash. This suggests a change in the demographic of buyers, possibly with a younger or financially-minded group being attracted to the model.
Despite its high price tag, the SF90 has held its value remarkably well in the resale market. This is somewhat uncommon for high-performance vehicles, which tend to depreciate quite substantially. It indicates a strong demand for the car, even after initial ownership.
One might expect the SF90's appeal to be primarily directed at established Ferrari owners, but surprisingly, roughly 30% of buyers are new to the brand. This signals the SF90's ability to draw in a wider customer base, demonstrating its ability to attract a broader audience beyond Ferrari's usual clientele.
Looking at the geographical distribution of sales, we see a strong bias towards North America, which accounted for close to half of all SF90 sales. This signifies the considerable influence this region holds on Ferrari's overall market strategy and its production planning for this model.
Interestingly, sales data suggests that the SF90 Spider variant was preferred by a vast majority of customers – about 80%. This preference for a convertible model, even within the highly specific niche of supercar buyers, is a noteworthy trend.
A key factor driving sales appears to be the high degree of customization available. Almost two-thirds of SF90 owners have chosen to personalize their vehicles, be it with unique color schemes or special performance options. This underscores the importance of individual expression and bespoke configurations within the luxury vehicle market.
It's remarkable that the SF90, with its initial base price of around $625,000, found a place among the most sought-after hypercars in the market. While it's on the more affordable end of Ferrari's supercar range, it clearly captured the imagination of enthusiasts in 2024.
Finally, it's notable that the SF90 has managed to maintain strong market demand even with new, competitive models entering the market. It demonstrates that Ferrari's longstanding reputation and heritage still carry significant weight in consumer decisions. This underscores the power of brand loyalty and established prestige in the supercar realm.
Ferrari SF90 Production Unraveling the Numbers Behind the Supercar - Component Sourcing and Supply Chain Logistics
The production of the Ferrari SF90, a groundbreaking hybrid supercar, hinges on a complex web of component sourcing and supply chain logistics. The car's unique blend of a potent V8 engine and cutting-edge electric components necessitates sourcing a variety of specialized materials. This includes things like carbon fiber and high-performance alloys, all crucial for upholding the SF90's performance standards. However, relying on these materials exposes the production process to potential disruptions in the global supply chain, which can impact production schedules and ultimately, Ferrari's ability to meet its quality and delivery targets.
Adding another layer of complexity, Ferrari uses a 'just-in-time' manufacturing approach. This means components are delivered to the assembly line as they're needed, reducing storage costs but also emphasizing the importance of a highly efficient and responsive logistics network. Any hiccups in getting the right parts at the right time can cause major issues. Ferrari has to carefully manage its supply chain to ensure that the precise components are delivered exactly when they are needed.
While the SF90 represents Ferrari’s commitment to both peak performance and more sustainable practices, navigating these intricate sourcing and logistical challenges is vital. This delicate balancing act is representative of the broader industry shifts towards electrified powertrains, making the SF90 a significant model in an evolving automotive landscape.
The Ferrari SF90's production hinges on a complex web of component sourcing and supply chain logistics. Ferrari relies on specialized suppliers for components like high-performance brakes and intricate electronic systems. The challenge is that these often involve unique technologies not widely available, potentially causing delays.
Ferrari's use of lightweight materials, especially carbon fiber, relies on a niche supplier base with limited production capacity. The availability of these materials can fluctuate, especially during times of global supply chain instability, directly affecting production times and output limits.
The SF90's manufacturing includes advanced techniques like 3D printing, which is useful for creating intricate parts that would be hard to make using traditional methods. This optimizes weight and enhances structural properties. However, it also requires skilled operators and specialized equipment, adding another level to the supply chain.
Interestingly, the lead time for sourcing electrical components, particularly for hybrid systems, tends to be longer than for mechanical parts because of the strict standards for safety and performance. This irregularity requires meticulous supply chain forecasting to reduce the risk of production delays.
While Ferrari has strong relationships with key suppliers, it's also been shifting towards a more diverse supplier base. This is a wise strategy for minimizing risk and making the whole operation more resilient in the face of supply chain disruptions, particularly after the global crises in recent years.
Ferrari's "just-in-time" (JIT) manufacturing is efficient in reducing inventory and waste, but it also makes the factory highly sensitive to any supplier delivery problems. Even a small issue can cause costly production shutdowns.
Given the SF90's global presence, the supply chain is highly international, spanning multiple continents. This vast network increases complexity because of the geopolitical landscape and international trade regulations, increasing the vulnerability of the system.
A large percentage of the SF90's components require custom fabrication to meet exacting performance requirements. This tailored approach adds complexity and makes adhering to tight production schedules more challenging.
The SF90's hybrid nature complicates the supply chain even further. Ferrari needs to coordinate with suppliers of traditional internal combustion engine components as well as suppliers of electric powertrain parts, which are often found in different parts of the automotive industry.
Integrating the hybrid powertrain requires more than just sourcing the parts. Assembly line logistics also need to adapt to the distinct requirements of both electrical and mechanical components. Moreover, assembly staff needs specialized training, highlighting the need for a skilled and adaptable workforce in such a specialized manufacturing environment.
Ferrari SF90 Production Unraveling the Numbers Behind the Supercar - Environmental Impact of SF90 Production Process
The production of the Ferrari SF90, while showcasing impressive performance, also raises questions about its environmental footprint. Ferrari's pursuit of sustainability is evident in its use of advanced engineering and materials like lightweight aluminum and carbon fiber, which help reduce resource use and emissions during the manufacturing process. The inclusion of a hybrid powertrain is a notable step towards lowering the overall environmental impact compared to traditional supercars. Further, Ferrari's efforts extend to a circular economy approach, focusing on recycling materials and minimizing waste. However, integrating the intricate electric components and sourcing the specialized materials presents challenges that can affect production timelines and the car's ultimate impact on the environment. The ongoing discussion about the SF90's production revolves around Ferrari's efforts to reconcile high performance with the need for environmentally conscious practices.
The Ferrari SF90 Stradale's production relies on components manufactured to extremely tight tolerances, down to 0.01 mm. While this precision is essential for performance, it significantly complicates the sourcing and assembly process. It's noteworthy that Ferrari outsources the production of its carbon fiber components to specialized suppliers. These suppliers only produce a limited quantity yearly, which can lead to delays and scheduling adjustments during the manufacturing process.
The SF90 incorporates advanced bonding techniques, using adhesives to join components instead of traditional welding. This reduces weight and improves rigidity, but requires meticulous control over the environment to ensure the adhesive properly cures and bonds. Despite the car's cutting-edge hybrid powertrain, the majority of its electrical components are sourced from established automotive suppliers. This demonstrates a degree of practicality in Ferrari's approach – they integrate these components into their unique assembly line, which shows the adaptability present in modern automotive engineering.
However, the unique cooling requirements of the patented MGU-K (Motor Generator Unit-Kinetic) pose a production challenge. Ensuring ideal thermal management during assembly adds complexity to the production process. Maintaining an exceptionally clean assembly environment is also critical for the SF90’s production. The factory has stringent standards in place to prevent contaminants from affecting performance, but it puts pressure on the logistics chain as all components must be free from debris or particulate matter.
The SF90 production utilizes a modular approach, where various subassemblies are built before integration into the complete car. This method allows for concurrent manufacturing steps, but can also lead to challenges in quality control if the different parts aren't perfectly matched. A large portion of SF90 customers opt for customization, making the supply chain particularly dynamic. This desire for bespoke cars adds uncertainty to production schedules as unique parts often need more time to source.
The sophisticated hybrid powertrain requires a hybrid assembly line. Both electrical and mechanical tasks are performed concurrently, necessitating a highly skilled workforce capable of transitioning seamlessly between assembly processes. Interestingly, despite the extended lead times typically associated with hybrid components due to regulations and performance standards, Ferrari seems to have mitigated some of these delays by cultivating strong relationships with its component suppliers, ensuring timely deliveries. This approach suggests a clear strategy of collaboration and foresight within Ferrari's manufacturing processes. While the SF90 demonstrates innovation, it simultaneously highlights the ongoing need for both engineering precision and robust partnerships in the manufacturing world.
More Posts from agustin-otegui.com: