Austin's East 17th Street Inside America's First Permitted 3D-Printed Home Community
Austin's East 17th Street Inside America's First Permitted 3D-Printed Home Community - Four Custom Designed Homes Built by Vulcan II Robotic Printer in East Austin 2024
The East 17th Street Residences in East Austin have become a proving ground for 3D-printed home construction, featuring four uniquely designed homes built by the Vulcan II robotic printer. These homes, designed by Logan Architecture, vary in size, offering configurations ranging from two to four bedrooms within footprints of 925 to 1,928 square feet. A key feature is the use of a specialized, disaster-resistant concrete mix, designed to handle harsh weather conditions. The development's significance lies in being the nation's first officially sanctioned 3D-printed residential community offering homes for purchase, starting at approximately $450,000. The homes themselves showcase innovative architectural possibilities, exemplified by the Treehouse Residence's design incorporating an extended top floor that serves as an awning for its patio. This project embodies the broader movement towards 3D-printed housing solutions, driven by the partnership between technological advancements and forward-thinking architecture and development. While 3D printing in construction is gaining traction, the East 17th Street project’s impact on the future of housing remains to be seen.
Four distinct homes have been built on East 17th Street in East Austin using the Vulcan II 3D printer. These residences, designed by Logan Architecture, vary in size, ranging from a modest 925 square feet to a larger 1,928 square feet, offering buyers choices from two to four bedrooms. Interestingly, these structures are built from a specialized concrete blend, intended to offer increased resilience in the face of severe weather events.
The East Austin community appears to be the first permitted 3D-printed housing development where the units are available for purchase in the US. Prices for these homes start at approximately $450,000. One of the homes, dubbed the Treehouse Residence, features a distinct top floor design that extends out to form a covered patio, providing an example of the design flexibility offered by 3D printing.
This project highlights the potential of advanced 3D printing in modern home construction. While 3D printing in housing is gaining global attention, this collaboration between ICON and 3Strands demonstrates the practical application of these technologies. It's important to continue to watch the development of these technologies, particularly considering aspects like the long-term performance of the materials and the evolving regulatory landscape surrounding 3D-printed construction.
Austin's East 17th Street Inside America's First Permitted 3D-Printed Home Community - Walls Made of Lavacrete Take Shape in 10 Days Rather Than Traditional 60 Day Build
The construction timeline for homes built with Lavacrete is dramatically shortened, taking only 10 days compared to the usual 60-day timeframe for traditionally built structures. This accelerated pace is a defining aspect of the East 17th Street development in Austin, a project that has garnered national attention as the first permitted 3D-printed residential community in the United States. The specialized Lavacrete, a proprietary concrete mixture, not only reduces construction time but also contributes to the homes' enhanced resilience against environmental factors. The design principles for the "House Zero" model, a project that prioritizes both durability and environmental responsibility, suggest that this new technology could become a viable means for achieving efficient and sustainable housing solutions. While there are many hurdles to overcome, the innovative construction methods demonstrated here are undoubtedly generating a considerable amount of interest and optimism for the future of home building.
The East 17th Street project demonstrates a fascinating shift in construction timelines with the use of Lavacrete. This specialized concrete material allows walls to solidify and reach a usable state in a mere 10 days, a dramatic improvement over the standard 60-day timeframe required for traditional concrete builds.
One of the interesting facets of Lavacrete is its blend of rapid curing with a focus on durability. The composition includes elements designed to withstand significant pressures, making it particularly useful in environments susceptible to severe weather or natural disasters.
ICON's Vulcan II printer is the driving force behind this rapid construction. It meticulously deposits Lavacrete in layers, with a typical nozzle speed around 4 inches per second. This method of building allows for intricate and custom architectural designs that would be much more difficult or time-consuming with conventional construction techniques.
The efficiency of 3D printing translates to significantly reduced waste compared to traditional methods. Studies have shown that traditional construction projects can generate upwards of 30% waste, primarily due to material scraps and unused portions. With 3D printing, only the exact amount of material needed is used, minimizing this waste stream.
Furthermore, computer simulations play a critical role in ensuring the structural integrity of the Lavacrete walls. This allows for optimization of the wall design prior to printing, significantly enhancing their ability to withstand external forces. The even distribution of material during the layering process also offers potential advantages in thermal regulation, potentially contributing to greater energy efficiency in maintaining consistent indoor temperatures.
It's notable that the 3D printing process allows for on-the-fly adjustments during construction. This ability to make changes to the design while printing is nearly impossible in traditional methods after the foundation is set. Additionally, initial tests have shown that Lavacrete structures display an increased resistance to mold, fungus, and pests, suggesting a potentially more hygienic building material than conventional wood or drywall construction.
While offering benefits, the use of Lavacrete also presents some intriguing challenges. The rapid setting time, while advantageous, might potentially reduce the overall carbon footprint associated with concrete curing compared to traditional methods. However, the widespread adoption of this technology requires navigating a complex regulatory landscape. Current building codes are primarily based on traditional building methods, which means there is a need for a re-evaluation of standards and protocols as 3D printing becomes more commonplace in residential construction. It will be interesting to see how these regulatory bodies adapt and the long-term impacts on the building industry.
Austin's East 17th Street Inside America's First Permitted 3D-Printed Home Community - Living Areas Feature 10 Foot High Ceilings Mixed With Wood and Metal Elements
The interiors of the East 17th Street homes feature 10-foot high ceilings, creating a sense of spaciousness and airiness. These high ceilings, a prominent design element, contribute to a more open feel within the living areas. The use of a mix of wood and metal accents throughout the interiors enhances the overall aesthetic appeal, adding a modern and sophisticated touch to the spaces. The designers have taken advantage of the height to maximize natural light, contributing to a bright and welcoming environment. The increased ceiling height allows for interesting possibilities, like incorporating large lighting fixtures or even taller plants, which could potentially enhance the character and ambiance of each home. This combination of height and material choices underscores a contemporary approach to residential design, reflective of the pioneering spirit of this first officially permitted 3D-printed community in the United States.
The living spaces within these 3D-printed homes on East 17th Street in Austin feature 10-foot high ceilings, which, from an engineering perspective, offer potential benefits beyond aesthetics. The increased vertical space can contribute to better air circulation, potentially improving indoor air quality and comfort. As warmer air naturally rises, taller ceilings can facilitate a more even temperature distribution, possibly lessening reliance on heating and cooling systems. It's interesting to consider how the interplay of wood and metal elements in the design could influence thermal properties. Metal's high thermal conductivity contrasts with wood's slower absorption and release of heat, leading to potentially more balanced temperature fluctuations within the space.
However, this combination of materials also presents some design challenges. Wood and metal expand and contract at different rates in response to temperature changes, creating potential stress points that require careful consideration during the construction phase. Light-colored metal surfaces can reflect heat, whereas darker wood can absorb it. Architects might leverage this contrast to manage temperature differences within the living spaces. But this approach requires meticulous design to avoid creating thermal discomfort.
The taller ceilings can create what's known as the "heat stratification effect," where warmer air accumulates at the ceiling. While this can be addressed with effective ventilation or strategically placed fans, it's a factor that needs to be accounted for in the overall thermal design of the homes. The acoustics of a space are also significantly influenced by ceiling height. Different types of wood, some softer and more sound-absorbent than others, can be selected to tailor the soundscape within a room. Moreover, the inclusion of metal elements can impact electromagnetic fields within the home, raising considerations for the placement of electronic devices and potential design opportunities that need to be further researched.
It's intriguing how the structural integrity of these homes could potentially benefit from a well-planned combination of wood and metal. If properly engineered, this interplay of materials could contribute to a stronger and more resilient structure, offering added safety against forces like high winds or seismic activity. It will be fascinating to observe how the design and construction of future 3D-printed homes leverage the various properties of materials like wood and metal in response to environmental conditions and engineering challenges. This Austin project, as a pioneer in this space, paves the way for such explorations.
Austin's East 17th Street Inside America's First Permitted 3D-Printed Home Community - Zero Waste Construction Process Reduces Material Costs by 30 Percent
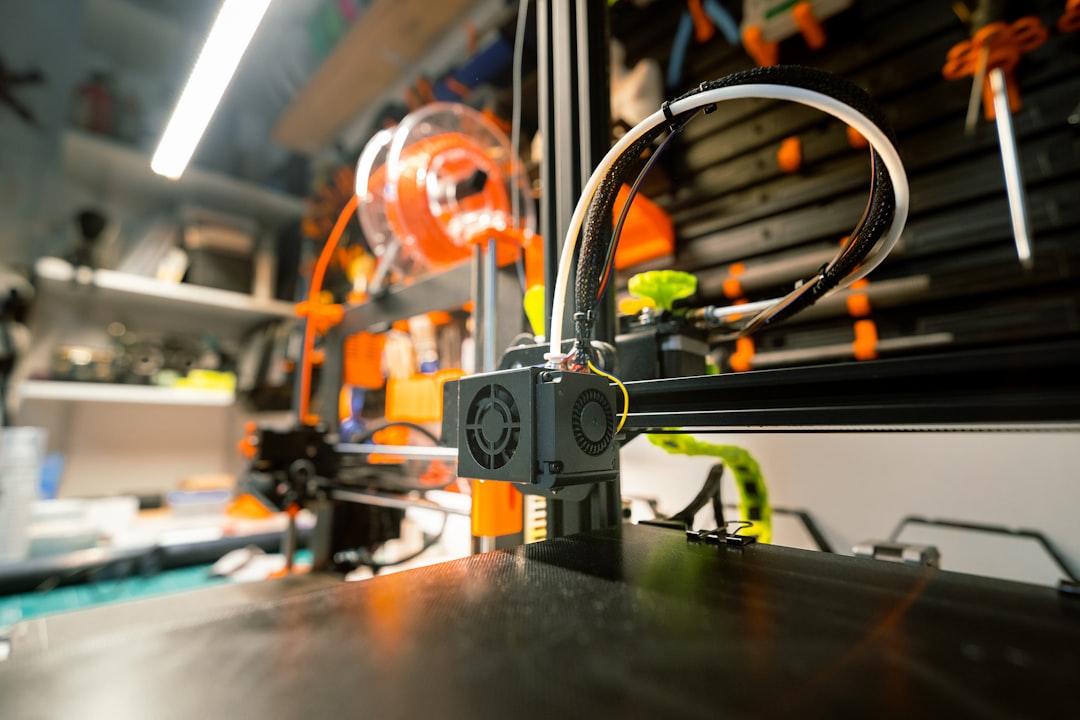
The construction process at Austin's East 17th Street community emphasizes a zero-waste approach, leading to a notable 30% decrease in material costs. This is a key aspect of the project, given Austin's overarching goal of achieving zero waste by 2040, a target that involves significantly reducing the amount of trash destined for landfills. The East 17th Street development, as the first permitted 3D-printed home community in the United States, serves as a demonstration of how innovative building practices can contribute to both cost-effectiveness and sustainability. This focus on waste reduction is part of a broader shift towards a circular economy in construction, an approach that prioritizes the reuse and recycling of materials to minimize environmental impact. While this innovative approach holds potential for reshaping the construction landscape, there are still hurdles related to adapting building codes and ensuring the long-term performance of the materials used in these 3D-printed homes.
The zero-waste approach employed in the East 17th Street construction process is noteworthy. It leverages the precision of 3D printing to minimize material waste, resulting in a 30% reduction in costs compared to traditional methods. Traditional construction often generates a substantial amount of waste – up to 30% from material scraps and unused portions. In contrast, the Vulcan II 3D printer uses only the exact amount of material needed for each layer, effectively eliminating the problem of excess materials.
This level of precision is achieved through the use of advanced design and modeling software which optimizes every aspect of the printing process, from material usage to structural integrity. The design process itself is focused on efficiency, ensuring the optimal amount of material is used for the intended purpose. This approach extends to the materials themselves, such as the specialized Lavacrete used in the East 17th Street homes. Lavacrete's composition enables stronger structures with fewer layers compared to conventional materials, reducing the overall amount needed for a given construction task. This highlights an interesting interplay between material science and construction methods.
Furthermore, the intricate architectural designs facilitated by 3D printing can be achieved without incurring the typical material costs associated with more traditional, labor-intensive detailing. Complex shapes and customized elements can be printed with minimal waste. Studies have indicated that conventional building methods can generate as much as 40% waste, mostly due to factors like cutting errors or mistakes made on-site. 3D printing's streamlined process minimizes these risks through its automated and precisely-controlled nature.
The rapid curing time of Lavacrete not only accelerates the building process but also significantly reduces waste at the construction site. Since the printer applies the exact amount of material needed, the need for on-site modifications or corrections is lessened. The process also enables the recycling of any excess Lavacrete, creating a closed-loop system where unused material can be reintroduced into the printing process, creating a ‘just-in-time’ supply of material.
Another intriguing aspect of this approach is the ability to adjust designs during the printing process. This flexibility minimizes the creation of excess materials due to poorly conceived initial designs. By refining designs in real-time, the need for pre-ordered materials is diminished, leading to lower waste. The zero-waste process positively impacts budget management, allowing project resources to be better allocated to other elements such as technology integration or design enhancements.
Finally, the future of this approach holds immense potential for even greater efficiency. Integrating artificial intelligence and machine learning into the design and printing processes could lead to further optimization of material usage. Algorithms could be developed to predict the most efficient material application strategies, ensuring that waste minimization remains a key goal of the engineering process. It's exciting to consider how AI-driven techniques could shape the evolution of 3D-printed construction in future projects.
Austin's East 17th Street Inside America's First Permitted 3D-Printed Home Community - Local Building Code Changes Allow for 3D Printed Load Bearing Walls in Austin
Austin has recently updated its local building codes to allow for 3D-printed walls that bear the weight of a structure. This change reflects the growing acceptance of innovative building techniques and coincides with the development of the first permitted 3D-printed home community in the United States located on East 17th Street. The updated codes, incorporating the 2021 International Building Code and recent amendments, provide a framework for utilizing new building technologies. These advancements in construction rely on automated systems for precise material placement in the walls, aiming for structural integrity and the development of more durable and efficient homes. However, this is a developing field. As 3D-printed home construction gains wider adoption, the effects on the broader building industry and the regulations that guide it are likely to be significant, and it remains to be seen how that all shakes out.
Recent changes to Austin's local building codes have opened the door for the use of 3D-printed load-bearing walls in residential construction. This is significant because it provides a framework for using these innovative materials and techniques while ensuring public safety. The code changes don't just say "yes, you can use 3D-printed walls"; they outline specific standards related to factors like earthquake resistance, wind loads, and how well the walls retain heat or cold. These standards are important, as the structural integrity of a building is paramount.
The Lavacrete used in the homes on East 17th Street isn't your typical concrete. It's engineered for superior strength and durability, often with added components to enhance its performance in various environmental situations, like extreme weather. While Lavacrete hardens quickly, which is a big advantage for speed of construction, it also needs careful control of environmental variables like temperature and humidity during the initial phases of hardening to reach its maximum potential. These environmental controls are crucial to avoid unexpected problems.
This rapid curing process is quite remarkable, with walls achieving a usable state in just 10 days compared to the usual 60-day timeframe for traditional concrete. However, the change in the construction process significantly reduces the need for traditional manual labor, like bricklaying and wood framing. This shift in labor requirements is something to keep in mind as this technology is adopted more widely.
The Vulcan II 3D printer provides a high level of precision in construction, enabling the creation of detailed architectural elements like curves and complex joins that would have traditionally required significant effort with scaffolding and skilled labor. This level of customization might also provide better design and functional outcomes for the homeowner but introduces new challenges when thinking about construction schedules and labor dynamics.
One unique aspect of this 3D-printed construction is the ability to make alterations to designs during the printing process. It's like being able to tweak a design while it's being built—a feature that's not possible with traditional construction methods. This offers a level of adaptability not available before, which can lead to fewer errors, less waste, and a more efficient process overall, which is important for sustainability.
Furthermore, the process used for the walls allows for insulation to be integrated directly into the Lavacrete mix. This can potentially lead to better energy efficiency within the home compared to traditional construction where insulation is often added as a separate layer, improving thermal performance and reducing the need for extra steps.
Preliminary findings suggest that houses built with 3D-printed walls might offer better energy performance. This may stem from the uniformity and density of the walls, which may result in reduced heating and cooling demands. The significant mass of the Lavacrete walls also gives them thermal mass properties, meaning they can absorb and release heat more effectively, potentially contributing to more stable indoor temperatures and less energy usage over time.
The increased use of 3D-printed construction will necessitate adaptations to building codes. These building codes are the safety and performance guidelines that homes must meet. Building codes need to be updated and adjusted not only to accommodate the new materials and technologies used, but also to implement safety and performance assessments specific to these 3D-printing techniques. This process will be vital as we transition toward a wider adoption of 3D printing technologies in the construction industry.
More Posts from agustin-otegui.com: