The Hidden Dangers of Corrosion in Parking Garage Stairwells A 2024 Safety Analysis
The Hidden Dangers of Corrosion in Parking Garage Stairwells A 2024 Safety Analysis - Reinforcement Bar Failure Causes Fatal Stair Collapse at Michigan State Garage March 2024
In March 2024, a Michigan State University parking garage experienced a devastating stairwell collapse that tragically claimed the lives of four individuals and injured twenty more. This incident, occurring during ongoing construction on the eighth level, was primarily blamed on the failure of the reinforcing steel within the concrete structure. The collapse, impacting five levels of an external section of the ten-story garage, highlighted the hidden dangers of corrosion in reinforced concrete. The deterioration of steel reinforcement, a common cause of structural failure, can lead to weakening, cracking, and ultimately, catastrophic collapses. It's crucial to recognize that corrosion can be accelerated by environmental elements and the presence of differing metals, which can create conditions for its rapid progression. This incident, similar to past failures in other structures, illustrates that even seemingly strong and durable structures can succumb to the silent threat of corrosion. Moving forward, a strong emphasis on evaluating and managing corrosion within these structures is needed to prevent future catastrophes. It serves as a wake-up call for the need for stricter safety protocols and proactive measures to protect against the often-overlooked issue of reinforcement corrosion.
1. The tragic collapse of the Michigan State University parking garage stairwell in March 2024 underscores the severe consequences of unrestrained corrosion on reinforcement bars. The loss of tensile strength in the rebar, which can be as high as 50% in severe cases, dramatically weakened the structure, ultimately leading to its failure.
2. The speed and extent of rebar corrosion are influenced by several environmental elements, notably pH levels, chloride concentration, and moisture content. In environments prone to de-icing salts, like many northern climates, corrosion can accelerate rapidly, greatly hastening degradation.
3. While concrete deterioration often shows up visually as cracking or spalling, the insidious nature of rebar corrosion can progress unnoticed until a severe event, such as the MSU collapse, occurs. This characteristic makes routine inspection and detection difficult and emphasizes the hidden danger associated with corrosion.
4. Current structural design standards might not always fully account for the potential severity of corrosion in challenging environments, possibly leading to inadequate protective measures being implemented. This could have shortened the service life of the Michigan State stairwell.
5. The incident serves as a stark illustration of how a structure's lifespan can be drastically reduced when maintenance protocols are overlooked. The Michigan State garage shows that without vigilant monitoring and preventative steps, concrete structures can prematurely fail due to corrosion.
6. Techniques like ultrasonic testing or half-cell potential measurements can identify corrosion early. However, these non-destructive testing approaches are not consistently implemented, possibly because of costs or a lack of understanding. This oversight leaves many structures vulnerable to unforeseen failures.
7. While innovations in concrete mixes improve durability in many ways, they may not effectively address the specific problem of corrosion damage. This creates a possibly misplaced sense of confidence in the long-term integrity of the structure.
8. Environmental elements, including temperature fluctuations and humidity, can significantly speed up the corrosion process in rebar, especially in structures facing frequent wet and dry cycles. This highlights the importance of assessing exposure factors when designing and maintaining structures.
9. Studies suggest that once corrosion starts within concrete, it spreads rapidly. Consequently, damage can become extensive before visual indications become apparent. This finding emphasizes the need for ongoing proactive monitoring methods to identify problems early.
10. The MSU incident not only raises concerns regarding the stairwell's design but also necessitates a reevaluation of current corrosion mitigation strategies. It appears that existing guidelines might not be adequately anticipating the challenges faced by structures in various real-world environments, potentially leading to inadequate protection.
The Hidden Dangers of Corrosion in Parking Garage Stairwells A 2024 Safety Analysis - Poor Drainage Systems Lead to Accelerated Metal Deterioration in Underground Levels
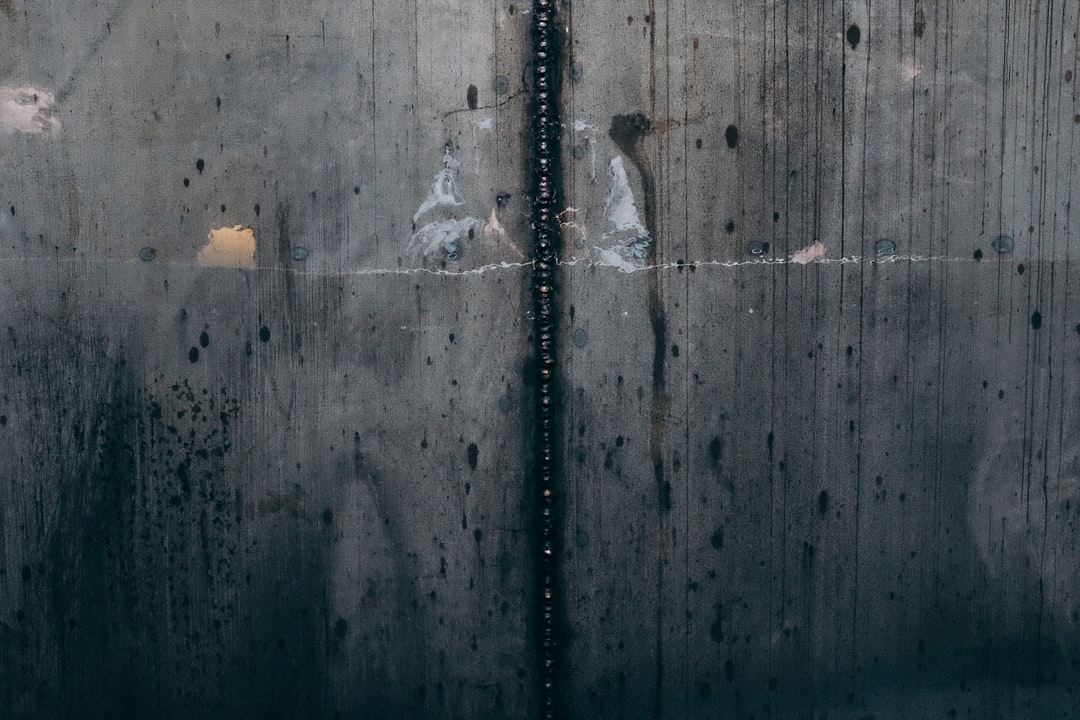
In underground environments, inadequate drainage systems contribute substantially to the accelerated corrosion of metal components. When water and corrosive substances are allowed to pool or linger due to poor drainage design or maintenance, the rate at which metal deteriorates increases significantly. This is especially problematic for structural elements like reinforcement bars found in parking garage stairwells. The issue highlights a broader concern within infrastructure maintenance – neglecting to consider the impact of environmental factors on critical components can have devastating consequences. Failing to properly address drainage issues not only poses a safety risk but can also significantly shorten the operational lifespan of underground structures that are constantly subjected to the corrosive effects of their environment. Therefore, careful planning, regular assessment, and proactive management of drainage systems are paramount to safeguarding the integrity and longevity of our underground infrastructure, including parking garages and their stairwells.
In underground environments, particularly those lacking adequate drainage, metal deterioration accelerates due to the presence of persistent moisture. Even a seemingly small amount of standing water, as little as 1 millimeter, can dramatically increase the rate at which corrosion progresses. This is concerning, especially given the often-overlooked nature of drainage in the design and construction phases of many parking garages.
The composition of the surrounding soil and water significantly influences the speed of corrosion. For instance, acidic soil or water containing high concentrations of chloride ions can alter the properties of concrete, making embedded metal components, like rebar, more vulnerable to corrosion. This is a factor that engineers should carefully consider in design choices.
Galvanic corrosion, a process where two different types of metal are in contact within a conductive medium like water, can lead to the degradation of one of the metals. Effective drainage systems can help minimize the risks associated with this phenomenon by limiting moisture availability. Furthermore, poorly functioning drainage can contribute to uneven electrical potentials within a structure, creating pathways for enhanced corrosion through electrochemical processes. This is particularly relevant for multi-level structures with a variety of metal components interacting within a complex environment.
The conditions found deep within underground levels, like those in parking garages, often present a perfect storm for accelerated corrosion. The combination of high humidity, limited ventilation, and stagnant water creates a favorable environment for microorganisms to thrive. These microorganisms can instigate microbiologically influenced corrosion, which can significantly damage rebar without any immediately apparent external indicators. It's unsettling that the process can be silently undermining a structure's integrity.
Poor drainage dramatically reduces the expected lifespan of rebar. Research suggests that unprotected rebar in these kinds of environments can lose a substantial portion (upwards of 15%) of its cross-sectional area within a mere five years due to corrosion. It highlights how quickly the unseen process can dismantle load-bearing components within a structure.
Water has the capacity to transport and deposit various mineral compounds. In areas with poor drainage, this can lead to the formation of a corrosive layer around the steel reinforcement. This layer can become more aggressive over time, further accelerating corrosion.
Often, during the planning and design of structures, the impact of drainage systems on corrosion is not thoroughly evaluated. This can result in the implementation of inadequate protection measures, which then leads to a higher potential for deterioration as the structure ages.
While concrete mixes often contain corrosion-inhibiting agents, their effectiveness can be significantly reduced in environments with poor drainage. Ongoing exposure to moisture can effectively neutralize these additives, leaving the rebar susceptible to unchecked corrosion. This can lead to a false sense of security in the long-term integrity of a structure.
The long-term cumulative impacts of inadequate water drainage can lead to unforeseen and potentially catastrophic consequences. For instance, soil erosion and the uneven flow of water can cause differential settling within a structure. This uneven settling creates additional stress points that further exacerbate corrosion and can potentially lead to cracks in unseen and inaccessible regions of a parking structure. It raises the question of how we can ensure structures are adequately protected from these insidious, but ultimately preventable, forms of deterioration.
The Hidden Dangers of Corrosion in Parking Garage Stairwells A 2024 Safety Analysis - Salt and Chemical Deposits Create Dangerous Air Quality Issues for Daily Users
Salt and chemical deposits, prevalent in urban environments, are a growing concern for air quality, affecting the health of millions of people daily. The widespread use of road salt, especially during winter months, contributes significantly to air pollution. As salt is aerosolized, it releases chloride into the air, negatively impacting air quality. This practice, while necessary for safe travel in some regions, exposes a substantial portion of the population—approximately 130 million Americans—to potentially harmful air. The implications for human health are troubling, with increased risks of respiratory and cardiovascular problems. Furthermore, the excessive use of road salt can lead to salinization of freshwater ecosystems, posing a serious threat to the environment. While the use of salt for de-icing is often considered essential, the long-term effects on both air quality and the broader environment demand closer scrutiny and possibly alternative approaches. The current practice highlights a critical need to re-evaluate de-icing strategies to ensure the balance of safe travel with protecting public health and ecological sustainability.
Salt and chemical deposits, frequently used for de-icing roads, introduce a concerning array of air quality and corrosion issues within parking garages, impacting those who use them daily. The presence of chloride, a byproduct of aerosolized road salt, infiltrates the environment and contributes to significantly degraded air quality. Millions of Americans are regularly exposed to these compromised air conditions, indicating the scope of this issue.
Beyond air quality, the intrusion of chlorides into concrete accelerates corrosion of the embedded steel reinforcement, especially in environments with high humidity. Chloride ions penetrate concrete more readily than water, damaging its structure and significantly speeding up metal decay. This effect is further heightened by the presence of heavy metals in runoff, which can interact with moisture and form a corrosive layer on the metal, leading to increased pitting corrosion and weakening the reinforcing bars.
The formation of efflorescence, a crystalline salt deposit, on concrete surfaces is a visual indicator of the underlying corrosion issue. It highlights the potentially unseen deterioration that is silently occurring within the structural components. Furthermore, the accumulation of corrosive dust, a consequence of both salt and other chemical deposits, can create an unhealthy atmosphere, especially in poorly ventilated areas, potentially leading to respiratory problems for regular users.
Research suggests that even seemingly minor increases in moisture content within the concrete can dramatically increase the rate of corrosion, indicating that humidity control is crucial in environments prone to de-icing practices. This reinforces the need for understanding how moisture, temperature, and chemical exposure interact to damage structures.
Adding another layer of complexity is the presence of corrosive salt spray near coastal areas, which interacts with existing corrosive agents and accelerates damage through intricate corrosion pathways. Not only does this salt contribute to corrosion, but it can also lead to the delamination of concrete surfaces, diminishing the critical bond between concrete and reinforcing steel, and significantly reducing the overall structural capacity.
The conditions created by stagnant water and the chemical deposits from de-icing solutions provide a perfect environment for the growth of certain microorganisms. These microorganisms can cause microbiologically influenced corrosion, further speeding up metal degradation without any apparent external signs of damage, making detection difficult.
Atmospheric conditions, like temperature fluctuations, exacerbate the impact of chemical deposits on air quality and accelerate material deterioration. These fluctuations can cause sudden spikes in air pollution, creating health concerns for garage users.
Alarmingly, research suggests that corrosion prevention strategies implemented in older parking structures might not adequately address current environmental challenges, making them vulnerable to the corrosive elements we’ve discussed. This means many structures built even a few years ago may fall short of modern standards for chemical exposure and air quality management, leading to significantly higher risks for both structural integrity and user health.
It's clear that a more comprehensive understanding of the combined effects of salt, chemicals, moisture, and atmospheric conditions is essential for developing effective solutions to mitigate the damage caused by corrosion in parking garages. We need a more nuanced approach to design, construction, and maintenance in parking structures, particularly considering the widespread use of de-icing salts and their environmental impacts. Otherwise, the risk of structural failure and detrimental impacts on public health will only continue to rise.
The Hidden Dangers of Corrosion in Parking Garage Stairwells A 2024 Safety Analysis - Outdated Building Codes from 1980s Leave 43 Percent of Structures at Risk
A significant portion of structures, roughly 43 percent, face heightened risks due to building codes that haven't been updated since the 1980s. A substantial number of communities, about 65 percent of US counties and municipalities, are still using these older codes. This failure to adopt more modern standards is estimated to lead to an additional $16 billion in property damage each year as a result of natural disasters. The lack of updated safety measures not only puts these buildings at risk during natural events but also contributes to potential issues with corrosion. Structures like parking garages, where corrosion can be significantly accelerated by the surrounding environment, are particularly vulnerable. It's clear that a review of current building codes and a more focused commitment to infrastructure safety is needed. Recent structural failures have shown that neglecting to address these issues carries a heavy cost, and the consequences of continued inaction can be dire.
1. A concerning 43% of structures built before the widespread adoption of updated codes in the 1990s are still operating under older standards. These older codes may not adequately address modern concerns about corrosion, making those structures potentially more susceptible to failure. It makes you wonder if these standards were ever really sufficient.
2. The projected service life of concrete structures often seems to be overly optimistic, especially given that corrosion can lead to failures within 20 to 30 years in harsher environments. The issue becomes particularly pronounced when building codes fail to emphasize the importance of using protective measures against corrosion. It makes me wonder if these design assumptions are truly validated by data.
3. A considerable mismatch exists between how a building is designed and its actual performance. Older building codes often underestimate the potential for localized corrosion, leading to unexpected repair costs and premature failures. This emphasizes the gap between theory and practice in the field.
4. Many parking structures built in the 1980s and earlier often lack the necessary features for effectively managing water flow and drainage. This can exacerbate corrosion problems by allowing moisture and harmful chemicals to accumulate in crucial parts of the structure. The failure to consider these conditions raises questions about what was considered essential back then.
5. De-icing salts, containing sodium chloride, have a greater ability to penetrate concrete compared to water. This increases the risk of corrosion, giving corrosive agents direct access to the reinforcing steel. It's interesting to consider how this unforeseen interaction has accelerated the deterioration of structures more than originally expected.
6. Modern construction techniques emphasize the use of corrosion-resistant materials. However, older codes offered no particular encouragement to utilize these advancements. This disconnect between current technology and building practices built using older codes creates an uneven playing field.
7. Chlorides can trigger electrochemical reactions that lead to galvanic corrosion, a phenomenon that was often overlooked in outdated building codes. These older codes typically assumed a more uniform rate of corrosion, not accounting for the complex interactions between different metals within a structure. It's concerning to consider that these interactions were not sufficiently considered in older designs.
8. Building inspections carried out under outdated codes may fail to identify key indicators of corrosion, such as moisture levels within the structure and the presence of efflorescence. This can lead to missed opportunities for early interventions, resulting in costlier repairs later on. We have to consider that inspections are only as good as the codes that guide them.
9. The risk of catastrophic structural failures is heightened in aging buildings that haven't been retrofitted to meet contemporary standards. Engineers suggest that the likelihood of these incidents increases when appropriate maintenance is not consistently performed. The question becomes: how can we effectively ensure that aging infrastructure is regularly assessed and brought up to modern standards?
10. Older building codes sometimes included insufficient protective measures against corrosion, giving a false sense of security to building owners and regulators. This can perpetuate the possibility of life-threatening structural failures within aging infrastructures. It emphasizes the need for continuously evaluating and updating codes as our understanding of these complex problems evolves.
The Hidden Dangers of Corrosion in Parking Garage Stairwells A 2024 Safety Analysis - Load Bearing Capacity Drops 30 Percent After Decade of Untreated Corrosion
Over a decade of neglecting corrosion in a concrete structure can significantly diminish its ability to support weight, causing a concerning 30 percent reduction in load-bearing capacity. This decline in strength weakens the overall structure and presents a serious threat to safety, particularly in crucial elements like stairwells found in parking garages. As the steel reinforcement inside the concrete corrodes, its ability to withstand tension weakens, making sudden and potentially devastating collapses more likely, as recent tragedies have demonstrated. It's clear that recognizing the severe, long-term consequences of corrosion is critical to maintaining the integrity and safety of these vital structures. To address this hidden danger, it's vital that we emphasize regular inspections and adopt proactive maintenance plans to prevent the devastating effects of untreated corrosion.
Over time, corrosion can significantly reduce a structure's ability to support weight. Research shows that, without treatment, structures can experience a 30% reduction in their load-bearing capacity after just 10 years. This raises major concerns about the safety of these structures, especially in places like parking garages.
Corrosion's effects are not always evenly distributed. Sometimes, rusting is concentrated in specific areas while other parts of the structure appear fine. This makes maintenance and inspection more challenging since the problem might not be obvious.
Furthermore, corrosion's pace doesn't follow a simple pattern. It tends to speed up as time goes on, particularly after the development of "corrosion cells." These cells can dramatically accelerate damage if left unchecked, leading to a rapid increase in the severity of corrosion.
In places like parking garages where there's a lot of traffic, physical wear and tear can make corrosion worse. This rubbing and abrasion can expose more metal to harmful substances and damage protective layers, speeding up the metal's deterioration.
Some studies indicate that small cracks in the concrete can act like channels for corrosive chemicals. This gives things like chloride ions a direct path to the reinforcing steel, making corrosion happen much faster.
The temperature within a parking garage plays a role in how quickly corrosion develops. Warmer environments generally make chemical reactions faster, and the temperature fluctuations parking garages experience can put stress on the materials, making them more likely to degrade.
It's crucial that the surfaces of materials are properly prepared during construction. If the reinforcing steel isn't cleaned and treated before being encased in concrete, it's much more vulnerable to corrosion at an early stage.
High-performance concrete is intended to withstand several types of damage, but it doesn't entirely eliminate the threat of corrosion. Unless environmental factors and preventative steps are thoughtfully integrated into the design, corrosion can still occur.
It's interesting to note that although concrete is usually thought of as resistant to corrosion, the presence of moisture and contaminants from parking lots can create a very corrosive environment. This combination can be especially damaging to the reinforcing steel bars.
Often, the long-term effects of corrosion are not considered adequately during the initial design stages. Engineers tend to focus on immediate structural requirements, potentially overlooking the severe and rapid impact corrosion can have over time. This underestimation of corrosion risks could be problematic in the long run.
The Hidden Dangers of Corrosion in Parking Garage Stairwells A 2024 Safety Analysis - Moisture Trapped Between Concrete Layers Creates Progressive Structural Damage
Moisture trapped between concrete layers, often a hidden and insidious problem, can gradually cause significant damage to the structure, particularly in environments like parking garages where stairwell integrity is paramount. This trapped moisture can initiate a series of detrimental effects, including delamination—the separation of concrete layers—and the development of cracks, which compromise the structural soundness. In addition, the presence of moisture frequently leads to mold growth and may cause warping of any overlaying materials like flooring or finishes. This issue highlights the critical role that effective moisture management plays in safeguarding concrete structures.
Beyond these direct impacts, moisture significantly accelerates the process of corrosion in embedded reinforcement bars. This accelerated corrosion, often exacerbated by environmental factors like de-icing chemicals and the presence of various metals, further weakens the structure's capacity to withstand stress and load. This phenomenon emphasizes the need for comprehensive and well-planned strategies to protect against moisture intrusion and its effects. Implementing measures such as moisture barriers during the initial design and construction phase can greatly enhance the durability and extend the lifespan of concrete structures, ultimately contributing to enhanced safety and resilience.
1. Moisture trapped within the layers of concrete provides an ideal environment for corrosion processes to begin, often weakening the structure long before outward signs of damage become apparent. This can lead to the corrosion of reinforcing steel, diminishing the structure's capacity to support loads.
2. Moisture intrusion between concrete layers can cause delamination, a condition where the layers separate. Over time, this can lead to extensive damage as the bond between the concrete and the embedded steel reinforcement deteriorates.
3. Research suggests that trapped moisture can not only accelerate the rate of corrosion but also contribute to the formation of expansive corrosion byproducts, which can generate significant internal pressure. This pressure can cause cracking and surface deterioration, increasing the likelihood of structural failure.
4. If soluble salts are present in the trapped moisture, they can worsen corrosion by establishing localized electrochemical cells. This results in concentrated corrosion on the reinforcement bars, potentially causing more harm than uniform corrosion across a surface.
5. Trapped moisture can lead to a type of corrosion called microbiologically influenced corrosion (MIC), where bacteria thrive in damp environments and accelerate the degradation of structural components. This type of corrosion can remain hidden until significant damage has occurred, making it challenging to address through maintenance.
6. Moisture entrapment can interfere with heat transfer through the concrete layers, a phenomenon known as thermal bridging. This can lead to variations in temperature that further accelerate corrosion and compromise the structure's overall durability, especially in parking structures subject to varying climates.
7. If concrete slabs are stacked without proper drainage, hydrostatic pressure can build up, forcing moisture through the concrete and worsening corrosion problems. Observations suggest that ineffective drainage in parking structures is often linked to an increased occurrence of corrosion-related failures.
8. As concrete repeatedly absorbs moisture, it can become more porous over time, allowing moisture to become trapped more readily. This shift can shorten the effective lifespan of the concrete and increase maintenance costs as corrosion becomes more prevalent.
9. Regular maintenance and inspections with a focus on moisture control are crucial. Engineering analyses indicate that proactive interventions can significantly delay the onset of corrosion and extend the service life of parking garages, emphasizing the importance of treating moisture as a critical engineering consideration.
10. While some contemporary concrete mixtures claim to resist moisture penetration, these enhancements may not always fully counteract the intricate interplay between moisture and corrosion. Unexpected moisture entrapment can negate the expected benefits, potentially leading to overly optimistic estimates of a structure's lifespan.
More Posts from agustin-otegui.com: