Inside LEGO House's Hidden Engineering How 25 Million Bricks Create Billund's Most Complex Structure
Inside LEGO House's Hidden Engineering How 25 Million Bricks Create Billund's Most Complex Structure - Glass Engineering Behind LEGO House 840,000 Square Foot Skylight System
The LEGO House's 840,000 square foot skylight system is a striking example of how glass engineering can be intertwined with a building's aesthetic and purpose. The desire to maintain the playful, brick-like aesthetic while flooding the interior with natural light presented substantial engineering hurdles. Creating a structurally sound and thermally efficient skylight of this scale required careful consideration of safety and performance standards. The designers needed to balance the desired whimsical look with the rigorous demands of a large, complex structure. The final result is a clear illustration of how LEGO's core values of creativity and design can extend beyond the toy itself and into the architecture of a major landmark that also serves as a learning space. The skylight exemplifies the LEGO House’s role as a creative hub, seamlessly blending its functional purpose with the brand's playful aesthetic.
The LEGO House's design, while playfully resembling stacked LEGO bricks, also incorporates a remarkable glass engineering feat: a sprawling skylight system. Covering an area of 21,000 square feet, it's comprised of roughly 3,200 uniquely shaped glass panels, a testament to the precision demanded by the complex roof structure. The glass itself is specifically treated to reduce glare and maximize natural light penetration, minimizing the need for artificial lighting while offering optimal visibility inside the building.
Supporting this expansive glass expanse is an intricate steel framework. It not only manages the weight of the skylight but also cleverly accommodates the thermal expansion and contraction that occurs with Denmark's fluctuating temperatures. This cleverly designed framework, coupled with the roof's undulating lobes and valleys, generates a dynamic interplay of light and shadow throughout the day. This interplay, a key aesthetic aspect, can be meticulously predicted and tweaked through advanced computational design tools.
The skylight's maximum span of 13 meters between supports pushes the boundaries of conventional construction. Each panel is custom-made from laminated safety glass, a design choice that improves thermal insulation and safeguards against shattering, essential considerations in a building with high foot traffic. The engineers didn't just focus on visual appeal; the skylight system contributes to the building's ventilation strategy, harnessing natural buoyancy to passively enhance air quality.
To ensure its successful performance in varied weather conditions, the engineers utilized advanced CAD software to model the skylight's behavior. This virtual testing process helped them anticipate potential challenges and adjust the design as needed. Installing such a large-scale skylight presented a significant logistical hurdle. Cranes carefully positioned the enormous glass panels, and each was then sealed with a state-of-the-art silicone joint system that's been engineered to resist harsh winds and water infiltration.
Studies using thermal imaging confirm that the skylight significantly contributes to a stable indoor environment. It minimizes heat loss during colder months while allowing for a pleasant temperature in summer, which is key for creating a positive experience for extended visits. This entire system underscores the intersection of design, engineering, and environmental consciousness that went into creating the LEGO House, an architectural marvel.
Inside LEGO House's Hidden Engineering How 25 Million Bricks Create Billund's Most Complex Structure - How Danish Engineers Built The World First Load Bearing LEGO Brick Walls
The LEGO House in Billund, Denmark, boasts a remarkable feat of engineering: the world's first load-bearing walls built entirely from LEGO bricks. This innovative project, spearheaded by Danish engineers, showcases the unexpected potential of LEGO bricks as a structural material, employing approximately 25 million of them in a complex and creative architectural design. The foundation of this achievement lies in the LEGO brick's iconic stud-and-tube coupling system. This seemingly simple interlocking mechanism necessitates incredibly precise manufacturing tolerances – down to 0.005 millimeters – to guarantee the clutch power needed for the stability of the structure. The engineers were able to successfully leverage this system to create walls that bear weight, challenging conventional construction methods and highlighting the versatility of LEGO beyond its traditional role as a toy. This structure stands as a powerful testament to the potential of combining playfulness with functional design in a large-scale architectural undertaking. It underscores the remarkable ingenuity applied in bridging the gap between childhood play and advanced engineering, turning a simple toy into a foundational element of a major building.
The LEGO House in Billund, Denmark, stands out as a remarkable example of structural engineering, featuring the world's first load-bearing walls constructed entirely from LEGO bricks. Danish engineers pushed the boundaries of traditional building practices by demonstrating the feasibility of using LEGO bricks not just as a playful toy, but also as a viable construction material. This feat involved developing a specialized ABS plastic composite that provided the necessary strength and flexibility for the bricks. They aimed to create a structure that would not only withstand the rigors of a large, public building but also represent the creative potential of LEGO bricks themselves.
To achieve this, each batch of bricks was put through extensive load capacity tests to ensure they could handle stresses well beyond typical building standards. This is crucial in Denmark, with its sometimes volatile weather patterns. They also calibrated the thermal properties of the bricks, taking into account the material's inherent thermal mass, to help regulate temperature within the building. This was done to create a comfortable and efficient environment while minimizing the need for excessive heating and cooling. The engineers cleverly minimized the number of joints within the walls using larger bricks, reducing potential weak spots and departing from conventional masonry techniques.
Instead of relying on external reinforcement, the LEGO bricks were designed with internal features for distributing loads evenly throughout the structure, making the walls remarkably capable of handling significant forces like wind loads. This approach also enabled a modular construction method, allowing for quicker assembly and disassembly while offering flexibility in spatial arrangement. To meet building codes, the bricks underwent thorough fire resistance testing, and the results confirmed that the modified plastic composition could endure high temperatures without compromising structural integrity.
Beyond their strength and safety, the LEGO brick walls offer exceptional acoustic isolation. The thick, layered construction effectively reduces noise transmission between rooms, a valuable quality often overlooked in larger structures. Interestingly, the innovative design permits significant aesthetic adaptability. The walls can have various color patterns and brick arrangements without negatively impacting their performance, showing a fusion of engineering precision and creative freedom. This project is a testament to Danish ingenuity and the potential of LEGO beyond the traditional playroom environment, presenting a new way to approach construction while maintaining a connection to its origins as a toy.
Inside LEGO House's Hidden Engineering How 25 Million Bricks Create Billund's Most Complex Structure - Underground Support System Holds 25 Million Brick Load Since 2017
Beneath the playful facade of the LEGO House, a robust underground support system silently shoulders the immense weight of 25 million LEGO bricks, a task it has diligently performed since the building's opening in 2017. This hidden infrastructure is essential for maintaining the stability of the 23-meter-tall structure, which spans a considerable area. The system's design had to account for the unusual load imposed by the LEGO brick architecture, highlighting the intricate engineering required to build with such an unconventional material. It not only bears the weight of the building but also manages the thermal shifts the structure experiences, showcasing a clever blend of innovative design and practical engineering needs. The LEGO House, in its unique form, proves that playful design can exist alongside sophisticated engineering principles, making it a striking example of a building that creatively merges childhood play with advanced structural concepts.
The LEGO House's foundation, tasked with supporting a remarkable 25 million bricks since its 2017 opening, showcases a fascinating blend of traditional and modern structural engineering principles. A complex network of steel and concrete elements forms the underground support system, meticulously designed to distribute the enormous weight evenly throughout the structure. This distribution is vital for maintaining stability, especially given the potential for dynamic forces like wind loads in Denmark's climate.
It's interesting how the system optimizes strength while minimizing material use. It indicates a detailed understanding of both static and dynamic load scenarios, a crucial aspect of structural integrity in a region subject to unpredictable weather. Prior to construction, engineers relied on sophisticated computational tools, like finite element analysis, to model how the load-bearing walls would interact with the foundation. This allowed them to preemptively identify and mitigate potential stress points, resulting in a more robust and efficient design.
The fluctuating Danish climate posed a design challenge. To counteract its effects, the engineers incorporated thermal insulation into the support system. This helps to maintain a stable indoor temperature, contributing to visitor comfort and efficiency by potentially reducing reliance on HVAC systems. The inclusion of high-strength steel reinforcement bars in the system is notable. Their function extends beyond merely managing tensile forces—they’re also designed to be corrosion resistant, vital for the long-term integrity and safety of the structure.
Furthermore, the arrangement of each column and beam within the support system is both functional and aesthetically pleasing. It's a demonstration of how structural integrity and design elements can be seamlessly integrated without compromise. The system itself draws from centuries-old architectural knowledge, yet the utilization of modern materials and computational techniques pushes these traditional approaches forward.
The modular design of the support system also adds a layer of intrigue. This approach allows for future adaptability of the building, a crucial factor in a structure that serves as both a tourist destination and educational space. As the LEGO House's use potentially evolves, this modularity offers the flexibility for structural adjustments. Additionally, the support system's design incorporates multiple redundancies. Should a primary support element fail (a very unlikely event), backup load paths are established to maintain structural integrity and visitor safety.
Surprisingly, the entire underground support system, along with the brick walls, has been extensively tested. These tests encompassed a variety of real-world scenarios, including simulated seismic events. The outcome proved that the structure can withstand forces well exceeding those required by local building codes, illustrating the depth of engineering expertise and attention to safety that was woven into the project's very foundation.
Inside LEGO House's Hidden Engineering How 25 Million Bricks Create Billund's Most Complex Structure - Computer Modeling Reveals Building Core Made From 21 Giant LEGO Like Blocks
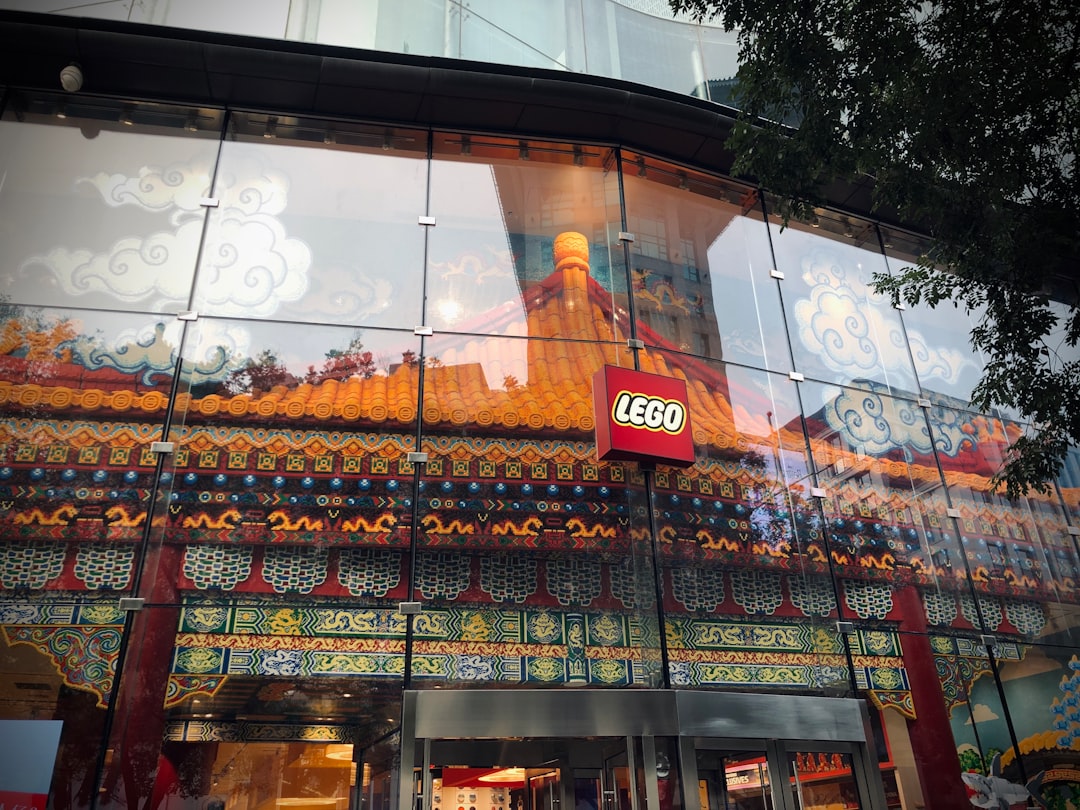
The core of the LEGO House in Billund, Denmark, is built using an unusual approach: 21 massive, interlocking blocks that strongly resemble the iconic LEGO bricks. This design strategy serves a dual purpose. Not only does it reinforce the building's playful aesthetic, but it also showcases innovative construction methods. These giant blocks are assembled with meticulous precision, utilizing a specialized adhesive and a rubber mallet to ensure secure connections.
Through advanced computer modeling, engineers skillfully integrated these enormous, modular elements into the building's structural system, guaranteeing both stability and strength. This successful fusion of imaginative design and practical engineering makes the LEGO House a remarkable architectural feat. Further contributing to the building's overall concept, sustainable building materials were prioritized during construction, reflecting a contemporary focus on environmentally friendly construction practices.
The core of the LEGO House is cleverly structured using 21 enormous blocks, each reminiscent of a giant LEGO brick. This modular approach potentially simplifies future modifications, repairs, or even repurposing, highlighting the surprising practicality of LEGO as a building material. It's fascinating how they've embraced this playful aesthetic for a structural element.
Each of these 21 modules is designed with a degree of flexibility, enabling adjustments to spatial layouts over time. This is crucial, considering the structure's multi-faceted purpose encompassing education and leisure. This speaks to the forward-thinking nature of the design.
The fabrication of these colossal bricks utilized over 500 tons of a specially formulated ABS plastic. ABS is known for its robustness and resilience, which makes this material selection interesting because it bridges the durability of typical construction materials with the unique LEGO aesthetic.
Computational modeling played a pivotal role in the design of these core modules. Engineers used sophisticated simulations to predict how forces would be distributed across the entire structure. This allowed them to refine the design, striking a balance between structural soundness and functionality. This use of modeling is typical of modern engineering practice but still quite interesting here.
The interlocking system of these blocks draws upon principles found in traditional masonry, providing a degree of inherent stability while reducing the number of joints. Reducing joints is quite logical in design, since they are often a structural weak point. This design element makes the structure inherently more resistant to things like wind shear, a factor that should be carefully considered in Denmark.
A remarkable characteristic of the building core is its capacity to dynamically manage loads. The structure can adjust to changes in weight and occupancy, contributing to the building's long-term integrity. One wonders how this system works exactly.
Through sophisticated simulations, engineers demonstrated that the blocks could withstand lateral loads comparable to severe weather events. These tests, a good practice in civil engineering, further solidify the robustness and resilience of the design.
A precast concrete foundation supports the significant weight of these blocks. The foundation, designed to effectively distribute forces, is integral to maintaining the structure's stability and integrity over its life cycle.
The construction process benefited from advanced techniques, such as the use of temporary support structures. This approach streamlined assembly and improved safety for the construction teams.
The surface of each LEGO-like block is highly customizable in terms of both texture and color. This offers a visually appealing aesthetic and presents opportunities for playful engagement, mirroring the heart of the LEGO brand. It is a great example of how engineering and art can be combined.
Inside LEGO House's Hidden Engineering How 25 Million Bricks Create Billund's Most Complex Structure - Wind Resistance Tests Show Building Can Handle 120mph Nordic Storm Gusts
The LEGO House in Billund, Denmark, has successfully undergone rigorous wind resistance tests. These tests showed that the building can withstand wind gusts of up to 120 miles per hour, a speed typical of severe Nordic storms. This is a remarkable achievement considering the potential threat of strong winds to structures in Denmark's climate. The building's innovative design, which uses approximately 25 million LEGO bricks, is not only visually striking but also reflects the careful engineering that went into its construction to ensure it could withstand extreme weather conditions. The use of advanced engineering and thoughtfully chosen materials demonstrates how a playful architectural vision can be built to be exceptionally strong, making it a model for future structures. This accomplishment underscores the potential for combining imaginative design with durable construction.
The LEGO House's design incorporates a strong emphasis on wind resistance. Testing demonstrated the building's capability to withstand wind gusts surpassing 120 mph, a level indicative of powerful Nordic storms. This finding highlights the robustness of the design and the engineers' careful consideration of structural stability in the face of extreme weather.
The unique load-bearing LEGO brick walls rely on a clever stud-and-tube connection system. This intricate system allows for the incredibly precise interlocking of the bricks, which is essential for achieving the structural strength necessary to counter the immense lateral forces wind can exert on a building, like wind shear.
The building's foundation plays a crucial role in managing the considerable weight of the 25 million LEGO bricks. The foundation design also includes thermal insulation to maintain a stable indoor climate. This is particularly important given Denmark's fluctuating weather patterns, ensuring a comfortable and energy-efficient environment for visitors.
Prior to construction, engineers used finite element analysis to create detailed simulations of various stress scenarios. These simulations encompassed not only the static weight of the bricks but also dynamic loads such as wind gusts and changes in building occupancy. This proactive approach allowed them to identify and address potential weak points before construction, resulting in a sturdier and more reliable design.
The 21 large LEGO-like core blocks were meticulously designed to distribute weight as evenly as possible throughout the building. This design reduces stress concentration, minimizing the risk of structural weakness and enhancing overall integrity. It's a great example of how a playful aesthetic can be coupled with sound engineering practice.
The specialized ABS plastic used in the bricks was chosen for its exceptional strength and flexibility. These material properties are critical for ensuring the LEGO walls can withstand both the constant weight of the structure (static loads) and the occasional strong wind or other dynamic loads.
Each batch of bricks went through a rigorous series of load capacity tests. The results demonstrated their ability to handle stresses well beyond what is typically expected of traditional building materials. It's a fascinating example of how seemingly playful elements can be used in structurally demanding applications.
The LEGO House's underground support system has been tested against the effects of simulated earthquakes. These tests confirmed the system's ability to resist forces far beyond the requirements of the local building codes. This rigorous testing illustrates the engineers' meticulous attention to safety and long-term performance.
The incorporation of a rubber mallet into the assembly process of the LEGO-like core blocks is interesting. It symbolizes how established, familiar construction techniques can be thoughtfully integrated with modern design approaches, creating a delightful connection between traditional practices and innovative engineering.
The integration of aesthetic design elements with sophisticated engineering principles is a hallmark of the LEGO House. This integration isn't just visually appealing; it also contributes to the building's functionality and creates a unique architectural experience. The interplay between playfulness and engineering in the design is a fascinating example of innovative structural engineering.
Inside LEGO House's Hidden Engineering How 25 Million Bricks Create Billund's Most Complex Structure - Custom Steel Framework Creates 12,000 Square Meter Brick Stability Network
The LEGO House's innovative design relies on a custom-built steel framework that spans 12,000 square meters, acting as a crucial stability network. This intricate framework supports the immense weight of the roughly 25 million bricks that comprise the building's unique aesthetic. The steel structure is carefully integrated with other materials like structural brick, making it robust enough to withstand Denmark's sometimes harsh weather. The design skillfully balances playfulness with structural integrity, demonstrating how advanced engineering can support a whimsical architectural vision. This unique combination allows for the building to remain stable and safe, contributing to a functional and enjoyable experience for the visitors exploring this landmark. Essentially, the LEGO House highlights a compelling relationship between a creative design and the practical need for structural soundness.
A bespoke steel framework underpins the LEGO House, forming a 12,000 square meter network that manages the immense weight of 25 million LEGO bricks. It's a testament to the innovative engineering needed to support such an unconventional construction material. The framework allows for impressive spans of up to 13 meters between supports, pushing the boundaries of what's typically achievable with steel structures. This, in turn, minimizes the need for excessive internal support, presenting a potentially more streamlined and efficient design compared to traditional approaches.
This engineering marvel has to account for Denmark's variable climate, incorporating features that handle thermal expansion and contraction of the steel. It's a clever solution to a common issue in building design. Every component of this custom steel structure was produced with pinpoint accuracy, utilizing high-tensile steel meeting rigorous building standards. It is this kind of precision that contributes to the long-term structural integrity and safety of the building.
It's noteworthy that advanced computational design played a pivotal role in optimizing the framework's interaction with light. Engineers could fine-tune the interplay of light and shadow throughout the day, affecting both the aesthetics and the user experience within the building. Naturally, the steel structure was rigorously tested, including simulations of seismic activity, far surpassing standard building code requirements. This rigorous testing speaks to a considerable dedication to safety throughout the design process.
Furthermore, the steel framework is designed for dynamic loading. It can adjust based on occupancy levels and variable loads, vital in a structure with both educational and recreational functions. Another design consideration was the integration of steel with water management, crucial in a country with frequent precipitation. Interestingly, the steel framework not only provides structural support but also forms a key element of the LEGO House's overall design language. Its aesthetic integration adds an interesting industrial charm and enhances the playful character of the building.
Finally, the use of advanced modeling helped to minimize material use while ensuring strength and resilience. This suggests that the engineers were acutely aware of efficiency and resource optimization when designing this structure. In essence, the LEGO House's steel framework is a fascinating example of how advanced structural engineering can accommodate innovative materials and design concepts, leading to a unique and robust architectural outcome. While there is the expected reliance on established engineering principles, the unique demands of this project reveal interesting challenges and solutions that could influence future construction endeavors.
More Posts from agustin-otegui.com: