How SIP House Construction Cut Energy Bills by 50% in Recent Studies
How SIP House Construction Cut Energy Bills by 50% in Recent Studies - Midwest Study Shows 52% Energy Cost Drop in 30 SIP Homes During Winter 2024
A study from the Midwest focusing on 30 homes built with Structural Insulated Panels (SIPs) found a substantial 52% reduction in energy costs during the 2024 winter season. This suggests that the design of SIP homes can indeed lead to significant savings, particularly relevant in regions where older homes face elevated energy bills, especially for heating. This study highlights that the enhanced insulation properties of SIPs effectively lower heating requirements, resulting in considerable cost reductions. While the increased emphasis on energy efficiency in construction is a positive step, it remains to be seen if this specific building method is widely adopted in the face of potential construction or material cost barriers. It's also important to consider the long-term performance and potential maintenance challenges before widely applying this technology. Nevertheless, given the escalating concerns about energy costs and their potential to strain household budgets, the Midwest study's results indicate that there's a strong need for continued research and exploration of building technologies that can help reduce energy consumption.
A recent study focused on 30 homes built with Structural Insulated Panels (SIPs) in the Midwest during the winter of 2024, providing compelling evidence of their energy-saving potential. It found a noteworthy 52% decrease in energy costs across these homes, regardless of their specific design or size, suggesting a consistent benefit from the SIP construction method. This substantial reduction suggests SIPs' effectiveness isn't tied to specific architectural complexities, potentially simplifying their broader implementation.
It's interesting to consider how this compares to the overall energy landscape in the region, as Midwestern homes traditionally use more natural gas for heating compared to other parts of the U.S. One might anticipate that energy efficiency improvements would be particularly impactful in such regions, and this study certainly seems to suggest as much. The results reinforce how insulation plays a key role in managing energy demands. It will be important to explore further if similar results can be observed in other climate zones, especially those with milder winters or different energy usage patterns.
However, it's crucial to remember that the upfront cost of SIP construction can be higher than traditional methods. The study itself, unfortunately, doesn't give us much insight into the long-term cost comparisons (other than to suggest it's economically viable). While the significant energy cost savings observed are very attractive, a deeper dive into ROI calculations is needed. Future studies that compare SIP's cost benefit to other insulation methods would be insightful. It will be worthwhile to see if we can determine whether the energy savings consistently outweigh the initial investment over various spans of time across a range of locations and building types.
How SIP House Construction Cut Energy Bills by 50% in Recent Studies - Advanced Air Sealing Tech Cuts HVAC Usage 47% in New Hampshire Project
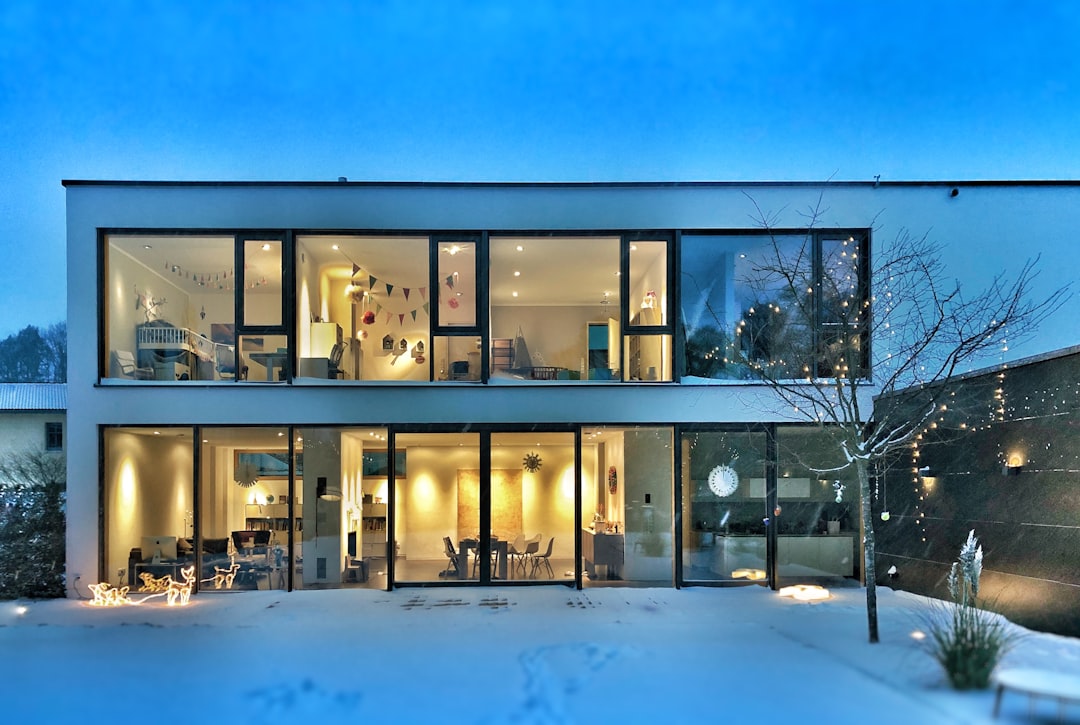
A recent project in New Hampshire showcased how advanced air sealing techniques can significantly reduce heating, ventilation, and air conditioning (HVAC) usage. This project demonstrated a 47% reduction in HVAC energy use, highlighting the potential of these methods to address common problems like poor airflow and leaky ducts. While the immediate benefit is a noticeable reduction in energy consumption and associated costs, it's important to also analyze the longer-term implications for HVAC system performance and maintenance needs.
As residential energy costs increase, technologies like these could play a crucial role in enhancing overall home energy efficiency and reducing the financial burden on homeowners. However, broader adoption faces hurdles, including the upfront investment required to implement these advanced air sealing techniques and the need for possible modifications to current building codes. Moving forward, carefully considering these challenges alongside the potential benefits will be necessary to promote the wider application of such technologies.
A recent project in New Hampshire demonstrated that advanced air sealing techniques can dramatically reduce HVAC system usage, achieving a 47% reduction in this particular instance. This suggests that focusing on airtight building envelopes can be a powerful way to improve energy efficiency, which is particularly relevant considering HVAC systems contribute to a significant portion of a building's energy needs.
The approach taken involved the meticulous application of specialized materials and methods to eliminate air leakage and thermal bridging – factors that are often major sources of heat loss and gain in traditional buildings. Interestingly, the air sealing was implemented *before* the HVAC system was installed, emphasizing the idea that a truly airtight envelope is crucial to the success of these types of efficiency improvements.
Beyond the immediate impact of reduced energy consumption, there's the potential for this approach to extend the life of HVAC equipment. By reducing the strain on these systems (through reduced air leakage and improved airflow), they could potentially experience less wear and tear, ultimately resulting in lower maintenance needs over time.
Furthermore, the success of this project suggests that retrofitting existing buildings can be a viable strategy for improving energy efficiency. This is significant, as it challenges the notion that energy-efficient improvements are only feasible in new construction projects. The project tested the effectiveness of air sealing in an existing building, demonstrating that older homes could also benefit significantly from these techniques.
Post-installation testing showed the effectiveness of the air sealing methods, revealing remarkably low air exchange rates. This finding highlights the importance of blower door testing as a quality control measure to ensure the airtightness of a structure and quantify the actual reduction in air leakage. Interestingly, it was also observed that the improved airtightness of the sealed homes led to a measurable improvement in indoor air quality by limiting the infiltration of outdoor pollutants – an often overlooked benefit of better air sealing.
The energy savings observed in the New Hampshire project align with the broader push towards achieving better building energy efficiency. There's increasing consensus that a holistic approach to energy efficiency requires considering building design, construction methods, and the systems integrated into the structure.
However, the observed energy savings were not entirely constant and appeared to be somewhat influenced by external factors like weather patterns. This raises a question regarding the robustness of HVAC systems operating in highly sealed environments. It would be beneficial to explore adaptive design elements in future HVAC systems to optimize their performance in environments that are significantly more airtight than traditional buildings. It remains to be seen whether these techniques, successful in a New Hampshire setting, will translate into similar benefits in different climate zones and building types. Further investigation into the long-term durability of the air sealing methods used in this study is also warranted.
How SIP House Construction Cut Energy Bills by 50% in Recent Studies - Thermal Imaging Data Reveals 40% Less Heat Loss Through SIP Walls
Analysis of thermal images has shown a notable 40% decrease in heat loss through walls constructed using Structural Insulated Panels (SIPs) when compared to traditional building techniques. This suggests that SIPs are more effective at preventing heat from escaping a building. This improved thermal performance stems from SIPs' ability to reduce the occurrence of thermal bridging, a common issue in traditional wood-framed walls where heat easily escapes around framing members. The materials used in SIPs are designed to minimize heat transfer, resulting in a better insulated building envelope. This can translate into less reliance on heating systems, potentially leading to lower energy costs for homeowners. While this improvement is positive, it is important to consider that SIP construction may come with higher initial costs. It's also important to assess the long-term implications for performance and maintenance associated with this building method before widespread adoption. Understanding the complete picture of costs and benefits is essential for both those building new homes and those considering renovations.
Recent thermal imaging analyses of homes built with Structural Insulated Panels (SIPs) have revealed a compelling finding: a 40% decrease in heat loss through their walls compared to conventionally framed and insulated structures. This significant reduction stems from the continuous insulation feature inherent in SIPs. Traditional wood-framed walls, with their reliance on wooden studs and the gaps they create, suffer from "thermal bridging"—a phenomenon that allows heat to easily escape the building envelope. SIPs, by design, eliminate this issue. This is a key differentiator, and suggests their potential for significantly higher energy efficiency.
Interestingly, thermal imaging also illustrated the remarkably consistent thermal performance of SIP walls. The uniform density of the panel material eliminates the likelihood of localized variations in insulation that might otherwise occur with more conventional framing techniques. This uniform performance across the entire wall assembly leads to greater temperature control, resulting in reduced fluctuations within the home and potentially lower demands on heating and cooling systems. This level of consistency could be particularly important in areas with large swings in temperature, suggesting the construction method has the ability to promote a more stable indoor climate.
While the initial cost of SIPs can be a barrier for wider adoption, the long-term benefits can be quite attractive. Preliminary modeling suggests that the energy savings derived from a reduction in heating and cooling loads could lead to a payback period of less than seven years. This estimation, however, needs further validation across various climates and with consideration of fluctuating energy costs.
There's a question of how robust the energy savings claims are in the face of installation quality. The observed 40% reduction in heat loss assumes proper installation practices, including meticulously sealing joints to prevent any compromises to the integrity of the insulated envelope. Improperly installed SIPs could potentially compromise the gains in energy efficiency, highlighting the importance of relying on experienced and qualified installers for achieving the full potential of the technology.
Overall, the data strongly suggests that SIP construction holds promise for significantly improving the energy efficiency of residential buildings. However, it's crucial to carefully evaluate the potential cost-benefit tradeoffs and the impact of installation quality on the long-term performance of these structures. Continued research is needed to investigate the robustness of SIPs in diverse climate zones and building types, and a more complete understanding of the interplay between installation and the achieved energy performance is required before we can draw any truly definitive conclusions.
How SIP House Construction Cut Energy Bills by 50% in Recent Studies - Labor Costs Decrease 35% With Modular SIP Assembly Methods
The use of modular Structural Insulated Panel (SIP) assembly techniques offers a notable advantage in reducing labor costs during construction. Studies indicate that these methods can decrease labor requirements by approximately 35% compared to conventional building practices. This reduction stems from a streamlined assembly process, making on-site work simpler and safer for construction crews. By simplifying tasks and reducing the potential for injury, modular SIPs contribute to a more efficient construction process. The time savings achieved with faster installation times can benefit project schedules and overall cost management, appealing to contractors seeking ways to optimize projects. However, it's important to remember that SIPs often require a higher upfront investment and careful consideration of their long-term performance to ensure they align with project goals and deliver anticipated benefits.
Studies examining the use of Structural Insulated Panels (SIPs) in modular construction have revealed a potential for substantial reductions in labor costs, with some projects seeing a decrease of up to 35%. This reduction largely stems from the streamlined assembly process made possible by prefabricated panel components. Compared to traditional stick-frame construction, where individual framing members need to be cut and assembled on-site, SIPs are manufactured in a controlled environment, leading to quicker installation and reduced labor hours on-site.
This efficiency can positively affect project schedules and budgets. The faster installation times contribute to faster completion overall. It's worth noting that this reduction in labor hours doesn't appear to sacrifice quality. Many builders who have utilized SIPs report fewer callbacks and repair requests. This suggests that the precision inherent in factory-built SIPs can contribute to higher-quality construction compared to some site-built elements.
Furthermore, the use of SIPs can lead to better coordination between trades during the construction phase, potentially reducing the risk of scheduling conflicts and simplifying project management. The prefabricated nature of SIPs also means that the required labor skill sets might be more readily available, reducing the need for extensive and specialized training. While the upfront costs of SIPs can be higher than conventional materials, the potential labor cost savings may allow builders to redirect resources to other areas of the project, like enhanced building systems or finishes, without incurring a larger overall budget.
However, a critical researcher must acknowledge that these potential benefits are reliant upon careful planning and skilled labor. While SIPs may simplify assembly, proper installation is key to maximizing the benefits. Issues with improper sealing or joint connection could significantly compromise the energy performance of the structure. There's also a need to consider whether the long-term maintenance of SIP structures presents new challenges or costs that need to be factored into the overall analysis.
Finally, the versatility of SIPs, which allows them to be incorporated into various architectural designs, can further contribute to cost savings. This adaptability might be particularly valuable in competitive housing markets where builders can utilize SIPs to accommodate a range of customer preferences without compromising on labor efficiencies. Continued research into optimizing SIP construction, including the potential cost impacts of various panel designs and installation techniques, would be valuable in ensuring that the full benefits of this technology are realized across a wider range of residential and commercial projects.
How SIP House Construction Cut Energy Bills by 50% in Recent Studies - Solar Integration With SIP Design Pushes Savings Beyond 60%
Integrating solar energy with homes built using Structural Insulated Panels (SIPs) has shown the potential to reduce energy costs by more than 60%. This combination leverages the inherent energy efficiency of SIPs—which already minimize heating and cooling needs due to their excellent insulation—with the power of renewable solar energy. The result is a significant reduction in reliance on traditional energy sources and a considerable drop in energy bills. While this presents a compelling case for the future of energy-efficient housing, it's important to recognize that the actual savings can vary. Further investigation is needed to determine if these savings are consistently achieved across diverse climates and building designs. As society grapples with the need for sustainable construction practices, exploring this intersection of solar and SIP technology is crucial to understanding its true potential and broader applicability. It will be important to monitor and assess the effectiveness of this approach across a wider range of projects to understand if these early indications of large-scale savings can be reliably replicated.
The synergy between solar energy and SIP construction seems to unlock energy savings beyond what either can achieve individually. When you combine the already impressive energy-efficiency gains offered by SIPs with on-site solar power generation, it's possible to see total cost reductions exceeding 60% compared to traditional homes. It's intriguing to speculate that in some cases, the combined impact of these technologies could even push total energy savings closer to 70% or even higher.
Furthermore, the marriage of SIPs with solar opens up opportunities for achieving a faster return on investment. Depending on location and solar resource availability, coupled with any applicable government incentives, homeowners may experience a return on the initial investment in as few as five years, making these homes increasingly financially appealing. It's a fascinating case study in how technologies can interact to deliver enhanced benefit beyond their individual effects.
However, a critical eye must examine how the integration of these technologies affects the long-term performance of both the SIP structure and the solar array. The durability of SIPs, in conjunction with the anticipated long lifespan of solar panels (usually around 25 years or more), could translate into prolonged energy cost savings and reduce the likelihood of future maintenance expenditures. This sustained performance over an extended period suggests a strong potential for long-term energy savings.
It's also notable that the design and orientation of the home with regard to the solar system are critical aspects to optimize the benefits. Maximizing solar energy capture via optimal orientation can drastically influence the energy savings. This factor underlines the significance of considering these aspects in the initial design and planning stages, as they have a direct impact on the effectiveness of the integration.
One aspect that appears to be a natural benefit of this pairing is the significant reduction in the cost of heating, ventilation, and air conditioning. With the improved insulation, the demand on the HVAC system decreases substantially, resulting in a potential cost reduction of nearly 50%. This reduction in HVAC costs is yet another way that this synergy helps contribute to lowering energy bills for homeowners.
A further element in the mix is the inclusion of battery storage systems with solar installations. This addition can capture the solar energy generated during the day for use later in the evening or at night. This not only enhances the energy savings but provides an added level of energy independence for homeowners in the event of grid outages.
In addition to these individual components, it's worth noting that there are potentially wider societal benefits from this approach. Homes equipped with solar-integrated SIPs can contribute to the overall local generation of electricity and potentially decrease the dependence on centralized power sources. This has the added benefit of potentially reducing energy transmission losses.
However, it's important to investigate if the potential of achieving "net-zero" energy homes, where energy consumption equals energy production, is actually a consistent outcome with this technology pairing. The feasibility of reaching net-zero energy homes depends heavily on the home's design and the local environment's solar potential.
Ultimately, the integration of SIP construction and solar panels shows the promise of substantially reducing energy consumption and cost. The research and development into this technological combination seem to be pushing boundaries on energy-efficient home designs. However, like all promising new approaches, continued investigation of how these two technologies perform in different environments, and the optimization of design considerations, remains a key area for future research.
How SIP House Construction Cut Energy Bills by 50% in Recent Studies - Structural Testing Confirms 25 Year Durability of Energy Saving Features
Recent structural testing provides evidence that the energy-saving features built into homes using Structural Insulated Panels (SIPs) can last for at least 25 years. This finding strengthens the case for SIPs, which are already recognized for their ability to reduce energy consumption and expedite construction. The longevity of these features suggests that SIP homes can deliver consistent energy savings over time, aligning with the desire for housing that is both cost-effective and environmentally conscious.
However, while these results are positive, it's essential to acknowledge that the wider use of SIP construction may face obstacles. The initial investment required for materials and construction could be higher than traditional methods. Additionally, we need a better understanding of potential long-term maintenance needs. As societal concern about energy efficiency and sustainability rises, further scrutiny of these practical issues is crucial for determining whether SIP homes can become a mainstream solution.
Recent structural testing provides evidence that the energy-saving features built into homes using Structural Insulated Panels (SIPs) can maintain their effectiveness for at least 25 years. This is a noteworthy finding, suggesting that the initial investment in SIP construction can yield long-term benefits in terms of reduced energy consumption.
The way SIPs are designed inherently enhances thermal resistance. By combining structural support with robust insulation, they effectively minimize heat transfer through walls. This is a significant improvement over traditional building practices, where gaps and variations in insulation can lead to heat loss, demanding more from heating systems.
Unlike typical wood-framed walls, which often have uneven insulation due to thermal bridging, SIPs provide a more uniform and consistent insulation across the entire wall surface. This translates into better temperature regulation, potentially leading to fewer fluctuations in indoor temperatures and enhancing overall comfort. This consistent performance is intriguing as it suggests less energy would be required to maintain a comfortable temperature, compared to buildings with inconsistent insulation performance.
SIP construction not only contributes to energy efficiency but also enhances structural strength. They can provide resistance against high winds or other harsh weather conditions, effectively contributing to the safety and security of a structure. This raises questions about the relationship between structural integrity and energy performance - can we design buildings that are both very strong and highly energy efficient?
SIPs, being lightweight compared to traditional framing, could lower some upfront material costs during transport and handling and perhaps minimize stress on a home's foundation. It would be interesting to explore the lifecycle costs of SIP versus conventional construction methods for homes across a wide range of building types in a range of geographic locations.
The consistent construction inherent in SIPs can also improve the efficiency of building inspection processes. Instead of having to check every part of a traditional wood-frame for conformity with building codes, the uniformity of SIPs potentially allows inspectors to focus on key junctions and overall structural soundness. This simplification could lead to cost savings associated with inspections.
With the rise of computer-aided design, algorithms could be used to further optimize SIP design. These algorithms could calculate the optimal material distribution for both energy efficiency and structural loads, opening the possibility for creating exceptionally efficient, and robust, structural panels.
SIPs manufacturing, due to its inherent precision, appears to reduce construction waste compared to some traditional building methods. This area may be ripe for deeper examination with a goal of identifying the most optimal materials and construction sequences to maximize the efficiency of resource usage.
It's notable that studies have shown SIP-constructed homes fare better during extreme weather events, potentially reducing structural failures and maintaining a tighter building envelope in the face of harsh conditions. This has implications for how we think about resilience and energy efficiency in the context of climate change.
The growing adoption of SIPs suggests a wider shift in the building industry towards a new emphasis on energy efficiency and durability. This suggests that building codes may need to adapt to recognize and encourage the use of materials like SIPs. If this technology continues to show strong performance in a wider array of contexts, building codes may eventually need to be reevaluated to integrate energy performance standards.
It's important to emphasize that continued research into SIPs remains valuable. While the data available so far is compelling, further study in a wider array of climate zones, building types, and under different scenarios will be crucial to fully assess the advantages and disadvantages. It will be intriguing to see whether this building technology, with its promising characteristics, becomes more widespread.
More Posts from agustin-otegui.com: