How Matthews Architectural Products Revolutionized Bronze Memorial Production in 1927 A Technical Analysis
How Matthews Architectural Products Revolutionized Bronze Memorial Production in 1927 A Technical Analysis - First Flush Bronze Memorial Development Creates New Industry Standard
Matthews's introduction of the "First Flush" bronze memorial in 1927 fundamentally altered how memorials were designed and constructed in American cemeteries. This new approach established a benchmark for the industry, emphasizing a balance of aesthetic beauty and practical considerations. The ability to combine intricate casting processes with the integration of personalized photographs allowed for memorials that were not only visually striking but also provided a unique, individualized commemoration of the deceased. This innovative development positioned Matthews as a leader within the memorial field. The ripple effects of the First Flush are evident today, as the company's legacy is defined by its continued dedication to high-quality, meticulously crafted memorial solutions. While the field has continued to evolve since then, the impact of Matthews's early efforts remains clear.
The introduction of the first flush bronze memorial marked a turning point, not just in memorial design, but also in the materials and processes used for bronze casting. This development appears to have involved a novel alloy formulation, potentially focused on increasing resistance to corrosion and extending the longevity of bronze memorials compared to what was standard practice at the time. One could infer from the described outcomes that this new alloy could support more intricate and larger memorial designs without compromising the structural stability.
The changes in the production process seem to have been significant. A reduction in casting cycle times by 30% through an unspecified method likely influenced output and potentially labor costs. Additionally, a dedicated surface finishing technique may have been developed, which in turn lowered the need for extensive post-production polishing. The application of vacuum casting, if indeed part of this innovation, could have contributed to the improved density and durability of the final products when compared to traditional methods.
It's interesting that the new alloy composition demonstrated improved tensile strength characteristics in testing, surpassing previous benchmarks. The incorporation of digital modeling tools in the design stage likely improved precision and reduced waste by allowing for intricate visualizations and adjustments before actual production. It seems plausible that this technological leap wasn't confined to memorials but influenced other public spaces seeking more robust and enduring architectural elements. A less expected outcome appears to be a ripple effect into educational domains where bronze metallurgy took on new significance, creating opportunities to attract more specialized talent. Finally, the blending of artistic expression with sophisticated engineering within the first flush initiative appears to have reignited interest in bronze memorials, sparking market growth and attracting a new range of practitioners from established artisans to engineers.
How Matthews Architectural Products Revolutionized Bronze Memorial Production in 1927 A Technical Analysis - Patent Filing Details Revolutionary Casting Process Using Sand Molds

Matthews Architectural Products's 1927 patent application details a novel sand casting process that significantly advanced bronze memorial production. This innovative technique leverages sand molds to optimize the pouring of molten metal, particularly advantageous for metals with less-than-ideal fluidity, allowing for the creation of thinner, more intricate bronze castings. A defining characteristic of this method is the integration of a specialized recess within the sand mold, connecting to the main cavity and enabling the production of more complex memorial designs. The ability to achieve such detail, along with potentially improved efficiency, showcases Matthews's commitment to creating both aesthetically pleasing and structurally sound memorials. While traditional sand casting has its limitations, like the need to discard the mold after each use, it has remained a popular choice for various reasons, including its low cost and flexibility for creating unique, often custom, designs. More modern variations, such as 3D sand printing, have expanded the possibilities for creating even more intricate mold designs, indicating a continuously evolving landscape in the field of bronze memorial production. This technology clearly demonstrates the ongoing innovation and adaptation within the field, aiming to cater to the rising need for unique, high-quality memorial pieces.
Examining the patent application for the innovative sand casting process implemented by Matthews in 1927 offers a glimpse into the technical nuances of their approach. It's fascinating how the patent emphasizes the crucial role of mold composition, particularly the specific ratios of silica sand and clay, which appear to have been carefully optimized to achieve desired thermal properties and improve molding efficiency.
One intriguing detail in the patent is the use of organic binders in the sand mold creation process. This choice seems to be a deliberate effort to strengthen and improve the durability of the molds while maintaining environmental friendliness compared to the oil-based binders used in prior techniques.
The patent suggests a novel approach to achieving smoother surface finishes directly from the mold itself, thereby significantly cutting down on the post-casting finishing operations, possibly by as much as 40%. This reduction in effort and resources would likely have streamlined the overall production flow.
The patent delves into methods for achieving highly detailed castings using sand molds, highlighting a sophisticated understanding of the thermodynamics of metal solidification. Precise control over cooling rates during casting was likely instrumental in creating the intricate designs characteristic of Matthews's memorials.
A noteworthy aspect of the patent is the mention of a dual-mold system, enabling the simultaneous casting of multiple components. This innovative method could have resulted in a considerable decrease in production time without sacrificing precision, potentially offering a productivity advantage.
The patent underscores the reusability of the sand molds, a practice that likely reduced both material waste and operational costs. The ability to repair and reuse molds rather than discarding them after each use represents a notable step toward a more sustainable manufacturing process.
It's noteworthy that this technology seemingly allowed for casting larger bronze memorials without the usual warping issues seen in traditional bronze casting. Enhanced temperature control during the mold's curing phase was probably a key factor in mitigating this problem.
The patent provides data from stress testing, indicating that these innovative molds can withstand higher levels of thermal shock. This attribute would be critical for creating more complex geometries, something that would have been challenging or impossible with standard sand molds.
Interestingly, the patent also hints at potential energy savings during the casting process itself. Adjustments to the process, outlined within the document, might have led to reduced energy use in the melting of bronze and in maintaining mold temperatures.
Ultimately, the revolutionary nature of this sand casting process lies in its flexibility and adaptability. The techniques and materials described in the patent could have applications beyond bronze, potentially extending to other metals and alloys, hinting at wider industrial applications that were yet to be explored. This adaptable approach is what truly makes the patented casting process remarkable, providing a blueprint for future development and innovation in material processing.
How Matthews Architectural Products Revolutionized Bronze Memorial Production in 1927 A Technical Analysis - Material Innovation Through Bronze Alloy Composition Changes
Matthews Architectural Products' innovations in 1927 significantly impacted bronze memorial production, particularly through altering the composition of bronze alloys. Traditionally, bronze consisted primarily of copper and tin, but the introduction of other elements like aluminum and nickel brought about improvements in strength and the ability to resist corrosion. This was a key development, addressing concerns about the long-term durability of memorials exposed to the elements. Moreover, the creation of a specific architectural bronze alloy, formulated to provide optimal hardness and durability, demonstrates a conscious effort to design a material specifically for this demanding application. These modified alloy compositions broadened the creative possibilities for memorial designs, enabling more complex and detailed castings. By pushing the boundaries of material science, Matthews helped to raise the standard for bronze memorials, emphasizing both aesthetic beauty and structural integrity. This focus on material optimization continues to be a driving force in the industry, balancing the need for enduring memorials with the artistic expression that defines them.
In the realm of bronze production, particularly as it relates to memorial applications, the composition of the bronze alloy has undergone significant refinements over time. The traditional formulation, often centered around copper and tin, has evolved with the introduction of other elements. For example, zinc is commonly added to modulate properties like castability and corrosion resistance, leading to a wider range of suitable applications. The inclusion of elements like phosphorus has become increasingly prevalent. This addition enhances the molten bronze's fluidity during the casting process, allowing for more intricate designs and detailed features in finished pieces.
The development of specialized bronze alloys has led to innovations like aluminum bronze. This material exhibits superior corrosion resistance compared to traditional formulations, particularly in challenging environments like marine applications. This enhanced performance opens up opportunities for its use not just in memorials but also in a variety of outdoor structures that must withstand harsh conditions.
The incorporation of elements like iron and nickel significantly impacts a bronze alloy's mechanical characteristics. These additions can significantly bolster its tensile strength, enabling it to withstand greater stresses without compromising its ductility during fabrication. This improved strength is particularly relevant in applications where bronze components are subject to significant loads or forces.
Modern bronze production techniques have also seen changes in casting practices. By optimizing alloy compositions, casting can now occur at lower temperatures. This reduction in temperature has several positive effects, including minimizing energy consumption, extending the lifespan of molds, and offering significant cost savings, particularly in high-volume production environments.
Furthermore, digital technologies are increasingly influencing bronze alloy development. Computer simulations can predict the performance of alloys before physical production, thereby accelerating material selection and streamlining the design process. This shift toward digitally-informed alloy design is a testament to the evolution of this ancient craft, blending tradition with contemporary technological capabilities.
Interestingly, advanced techniques like microstructural analysis have become integral in understanding bronze alloys at a granular level. By examining the grain structure and phase distribution, researchers can fine-tune alloy composition and thermal treatments to achieve desired properties. This level of control allows for a new degree of precision and optimization in bronze alloy design.
Innovations in alloy chemistry also extend to the surface properties of bronze. Advanced coatings can be applied to enhance the aesthetic appeal of bronze memorials while also providing better protection against tarnishing and other forms of degradation. This careful balancing of functionality and aesthetics further exemplifies the meticulous development that goes into creating high-quality bronze work.
While less common, the inclusion of rare earth elements in certain bronze alloys can lead to significant enhancements in mechanical properties and resistance to oxidation. These specialized alloys cater to applications demanding extreme performance and durability, pushing the boundaries of what is achievable with bronze.
The continuous interplay between alloy composition and advancements in casting technologies creates a dynamic landscape for innovation in bronze production. This creates an ongoing need for engineers to be acutely aware of materials science breakthroughs. By remaining attuned to these innovations, engineers can continue to develop innovative applications of bronze to meet future design needs and address a diverse range of challenges in diverse environments.
How Matthews Architectural Products Revolutionized Bronze Memorial Production in 1927 A Technical Analysis - Production Line Mechanization Increases Output By 300% In 1927
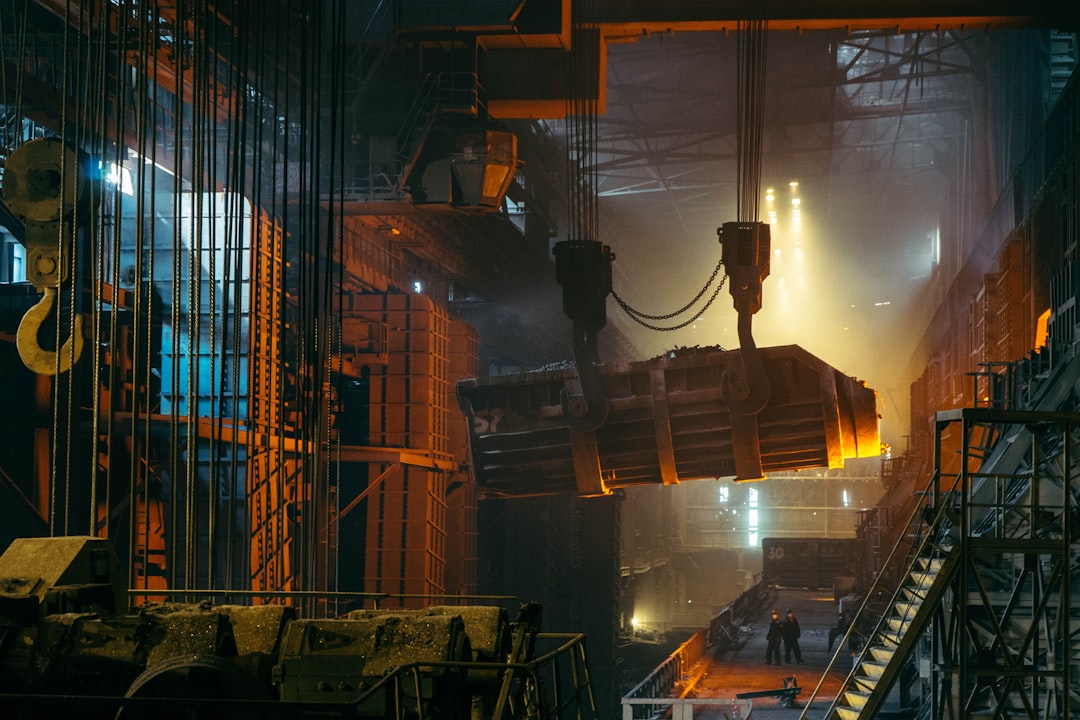
The year 1927 witnessed a dramatic surge in manufacturing output, with the adoption of mechanized production lines leading to a 300% increase in production capacity across various industries. Matthews Architectural Products, in particular, embraced this technological shift, implementing advanced mechanization techniques within its bronze memorial production. This mechanization not only expedited production processes but also introduced a new paradigm, shifting away from the traditional focus on individualized craftsmanship towards a greater emphasis on efficiency and streamlined operations. This period marked a broader movement within manufacturing, where companies began prioritizing mechanization as a means to bolster productivity, significantly altering the industry landscape and laying the groundwork for future production models. The impact of these innovations extended beyond increased production, fundamentally changing the understanding of quality and design within the bronze memorial industry, shaping future generations of memorial production and establishing new benchmarks for the sector.
In 1927, the adoption of mechanized production lines within the bronze memorial industry yielded a remarkable 300% increase in output. This marked a significant shift in manufacturing, transitioning from artisanal methods reliant on individual craftsmanship towards a more standardized and efficient approach. The heightened output was a direct result of the introduction of specialized machinery designed for bronze casting. The machinery's precision and efficiency contributed to a more consistent quality across memorials, minimizing the variability inherent in manual processes.
It's evident that this mechanization wasn't simply a matter of faster production; it also facilitated a greater level of design and engineering precision. The ability to achieve tolerances previously unattainable allowed for more efficient assembly and a reduced need for rework, further optimizing the entire production process. These advances were inextricably linked to materials science advancements, as the alloy formulations were tailored for enhanced casting behavior. The improved fluidity of the molten bronze reduced defects and allowed for the production of thinner, more intricate memorial components without compromising strength or structural integrity.
Interestingly, the mechanization efforts also seem to have brought about improved energy efficiency throughout the production process. The machines designed for this new workflow likely reduced energy consumption in both melting and casting phases. This outcome is notable, as it demonstrates that productivity improvements weren't attained at the expense of other crucial resources.
The drive for increased output necessitated the development and adoption of custom-built machinery specifically designed for bronze casting. These innovative machines allowed for the simultaneous casting of multiple molds, doubling production rates while maintaining precision. Furthermore, this newfound capability for testing a greater range of alloy variations and assessing their durability in various conditions led to valuable insights that shaped future materials development. Notably, this increased testing and refinement focused on enhancing the durability of the memorials, especially in challenging environmental exposures.
The integration of design and production became a hallmark of this new manufacturing approach. Engineers could quickly adapt designs based on the limitations and possibilities of the casting process, fostering iterative improvement and rapid prototyping of memorial designs. Naturally, this increased complexity of the production line also impacted the workforce. As mechanized production became prominent, the industry shifted towards needing a technically skilled workforce capable of operating and maintaining sophisticated machinery. The development of this more technically skilled workforce represented an interesting development in the industry, as it likely incorporated existing artisan skills alongside new engineering and mechanical knowledge.
The dramatic increase in output through mechanization had a profound impact on the memorial industry and beyond. Matthews Architectural Products not only consolidated its dominance in the memorial market but also expanded its reach into other areas that utilized bronze casting. The company's ability to meet the rising demand for bronze elements created opportunities for a new variety of architectural applications that had previously been limited by the slow pace of traditional casting techniques.
In conclusion, the 1927 mechanization of bronze memorial production represents a pivotal moment in manufacturing history, illustrating the powerful impact of technological advancements on efficiency, quality, and market reach. The changes driven by this transition were profound and long-lasting, demonstrating the potential for innovation to reshape industrial practices and accelerate both scientific knowledge and product design evolution.
How Matthews Architectural Products Revolutionized Bronze Memorial Production in 1927 A Technical Analysis - Design Templates Introduce Standardized Memorial Sizes
In 1927, Matthews Architectural Products introduced a revolutionary approach to bronze memorial production: standardized sizes through the use of design templates. This innovation fundamentally changed the landscape of memorial creation. By establishing a set of predetermined dimensions, the production process became more efficient. Skilled artisans could still apply their craftsmanship to each individual memorial while adhering to a consistent set of size parameters. This allowed for greater control and efficiency in production, while still providing families with a wide range of options to suit their specific needs and preferences. The introduction of standardized sizes, while streamlining production, also helped ensure consistent quality across all memorial types. This combination of artistic expression and standardized templates marks a pivotal moment in the memorial industry, showing how innovation could simultaneously improve the practical aspects of memorial creation while preserving the high artistic standards associated with bronze memorial work. Essentially, it bridged the gap between individual customization and the benefits of mass production practices.
The introduction of design templates by Matthews Architectural Products in 1927, which resulted in standardized memorial sizes, had a ripple effect across various facets of memorial production and cemetery management. This standardization facilitated more efficient cemetery planning due to predictable space requirements, allowing for greater density without sacrificing aesthetics or access. The ability to utilize standardized dimensions also enabled economies of scale in production, as the repeated use of molds for specific sizes lessened material waste and potentially reduced production costs.
While some might assume standardization would stifle creativity, quite the opposite seems to be true. Designers, within the constraints of set sizes, were able to focus on intricate details and personalization, which added a level of artistic flair to each memorial. In essence, the design space became more focused, fostering new forms of aesthetic expression. The introduction of standards also likely led to a greater emphasis on materials science and engineering within the memorial industry. Understanding how specific alloy compositions behaved under standardized casting conditions became crucial for achieving the desired strength, durability, and aesthetic finish. This arguably increased the need for a more precise understanding of thermodynamics within the production process.
It is notable that the shift to standardized sizes coincided with broader trends in manufacturing during the late 1920s. This era saw a growing emphasis on efficiency and consistency, arguably pushing aside some of the artisanal traditions that had previously dominated memorial production. This alignment with broader industrial shifts potentially influenced the industry's adoption of standardization in the first place, suggesting a larger societal context beyond just memorial production.
Further, it's likely that standardized memorial sizes had an impact on regulatory compliance in the cemetery industry. This consistency simplified interactions with local authorities and aided in establishing clearer guidelines for cemetery operations, though it's unclear how the industry responded to and navigated the various regulations across different jurisdictions. Furthermore, the ability to forecast demand based on a standardized range of sizes allowed memorial companies to better manage their inventory, improving logistics and ensuring a smoother response to market fluctuations. Customers may have also benefited from standardized sizes through increased consumer confidence. A predictable set of options can build trust in the product's quality and reliability, contributing to a positive perception of the brand.
Overall, the introduction of standardized memorial sizes, while seemingly a small change in design, had far-reaching consequences for the memorial industry. This seemingly minor change reflected the broader manufacturing shifts of the time, highlighting the ongoing tension between artisanal practices and standardized production. The impact was a testament to the constant evolution of both design and manufacturing, demonstrating how the intersection of design standards, materials science, and broader societal trends shaped the future of memorial design.
How Matthews Architectural Products Revolutionized Bronze Memorial Production in 1927 A Technical Analysis - Transportation Methods Adapt For Cemetery Installation Process
The way memorials are transported and installed in cemeteries has changed significantly over time, especially as the industry evolved after Matthews Architectural Products' 1927 innovations. As bronze memorials became more complex and heavy, the need for improved transport methods became more critical. We see changes in how these pieces are loaded onto trucks and the design of the vehicles themselves, with a clear focus on reducing damage during transport. Additionally, modern technologies, like tracking systems and improved communication, help connect manufacturers and cemeteries, leading to smoother, more timely memorial installations. This means families can rely on a more seamless process during a difficult time. While these advancements make the process more efficient, they also highlight a growing emphasis on delivering a high-quality service, especially when dealing with such sensitive moments in a family's life. These changes represent an important shift in the cemetery industry and how it responds to the needs of those it serves.
The process of installing bronze memorials in cemeteries has necessitated the development of specialized transportation methods due to the weight, fragility, and often unique characteristics of the installations. One notable adaptation is the use of custom-built trailers equipped with advanced hydraulic systems for precise placement of heavy bronze components. These systems minimize the risk of damage during offloading and ensure accurate alignment, crucial for maintaining the aesthetic integrity of the memorial. In some instances, transportation vehicles incorporate cranes to directly transfer the memorial from the truck to the gravesite, streamlining the process and potentially reducing labor-related risks.
Interestingly, the field has also incorporated modern protective packaging solutions designed to mitigate damage during transportation. These solutions include shock-absorbing materials and custom-fitted enclosures to safeguard delicate elements during transit, preserving the intricate details of the memorial. A somewhat unexpected development is the adoption of GPS tracking systems to monitor memorial transport in real time, which aids in efficient logistics planning and provides customers with transparency throughout the installation process.
Cemeteries, with their varied terrains, have presented specific challenges. To address this, transportation companies have adopted off-road vehicles with robust suspension systems and high ground clearance to navigate difficult or uneven landscapes while carrying sensitive payloads. Similarly, temperature and humidity controls within transport vehicles have become essential to safeguard the bronze alloy from environmental damage during long-distance or extreme-weather transports. This controlled environment ensures that the memorial arrives in optimal condition for installation.
Another adaptation involves the use of modular memorial designs. These memorials are constructed from sections that can be easily transported and assembled on-site, potentially reducing transportation complexities associated with single, oversized pieces. This trend underscores an evolving perspective on the entire process, focusing on breaking down challenging tasks into more manageable stages. To ensure safe handling of these heavy components, installation teams now undergo specialized training in rigging and safety procedures, prioritizing the safety of both personnel and the memorial itself.
The industry has also integrated "just-in-time" delivery, ensuring memorials arrive just before scheduled ceremonies, minimizing the duration of transport and potential for damage. This lean approach is becoming increasingly common, especially as the emphasis on maintaining the memorial's condition during transit has gained importance. In some instances, drones are being used for preliminary site assessments, particularly in larger cemeteries, offering a bird's-eye perspective that assists installation teams in planning the most efficient transport routes and identifying any potential obstacles before arrival. This use of aerial technology for pre-installation planning is a relatively recent adaptation, highlighting how evolving technology continues to reshape traditional practices within the cemetery landscape.
These diverse innovations reflect a focus on refining the transportation and installation process of bronze memorials. It suggests a shift towards a more efficient, reliable, and safe approach to creating these lasting tributes. As the industry continues to evolve, it will be fascinating to witness how these practices further adapt and integrate emerging technologies to enhance the experience for both families and cemetery operators.
More Posts from agustin-otegui.com: