Ford Engineering Laboratory Celebrates 100 Years A Century of Automotive Innovation
Ford Engineering Laboratory Celebrates 100 Years A Century of Automotive Innovation - 1924 The Birth of Ford's Engineering Hub

The year 1924 saw the birth of Ford's engineering core—the Ford Engineering Laboratory—in Dearborn, Michigan. This move signified a major shift in Ford's approach to vehicle development. Under the direction of Albert Kahn, the laboratory, a multifaceted engineering complex, finally opened its doors in 1930. Henry Ford saw this facility as vital, a place where tool design, production engineering, and experimental research were consolidated. The lab's importance was evident in its central role in the design and engineering processes at Ford. It's interesting to note that the building replaced Ford's former tractor manufacturing plant, reflecting the changing priorities of the company. This transition points to Ford's growing emphasis on automotive innovation and engineering.
The Engineering Laboratory, one of the largest such facilities in the automotive world at that time, saw numerous expansions over the years, mirroring the growth and changing needs of Ford's operations. Though Henry Ford himself had an office in the building, it was primarily a venue for him to engage with employees and visitors rather than a regular workspace.
Despite its changing role over time, the Ford Engineering Laboratory has maintained a remarkable legacy, contributing significantly to automotive innovation and product development for well over 90 years. As it nears its 100th anniversary in 2024, the laboratory remains a symbol of engineering achievements and design innovation within the automotive industry.
The year 1924 marked the genesis of Ford's engineering prowess with the establishment of the Engineering Laboratory in Dearborn, Michigan. It was a bold step, a dedicated space for pushing the boundaries of automotive technology. While Ford's name was already synonymous with innovation thanks to the Model T, this new facility represented a commitment to a more systematic approach to design and engineering. Architect Albert Kahn's design, though completed in 1930, embodied Ford's vision of a versatile workspace—a crucible where tool design, production engineering, and experimental research would converge. The land itself had a prior life, housing Ford's Dearborn Tractor factory, hinting at the company's evolving focus.
Henry Ford's own presence in the lab, though primarily as a host for visitors and staff meetings rather than a regular workplace, underscores the importance he placed on this new enterprise. The facility was undeniably substantial for its time, one of the automotive industry's largest engineering centers, signifying a shift toward more sophisticated design and development processes. Its aesthetic combined a classic exterior with a highly functional interior, the marble-floored lobby being a testament to a desire to create an environment conducive to innovation.
While the lab initially focused on enhancing the existing Model T, it simultaneously fostered a culture that would have lasting impact. It's interesting to consider that the lab's ambitions, though clearly linked to Ford’s commercial objectives, would ultimately contribute to broader developments in materials science, manufacturing methodologies, and vehicle safety. The Ford Engineering Laboratory serves as a reminder of the multifaceted nature of engineering progress, demonstrating the constant balancing act between technical possibilities and market realities—a tension that continues to shape automotive engineering a century later.
Ford Engineering Laboratory Celebrates 100 Years A Century of Automotive Innovation - 1950s Pioneering Automotive Safety Innovations
The 1950s marked a turning point in the automotive landscape, as safety concerns started to gain traction. While safety wasn't a primary focus in the early part of the decade, it began to emerge as a significant consideration. This period saw the introduction of several key safety features, including seat belts, which quickly became a standard in vehicles. Their adoption played a crucial role in mitigating the severity of injuries during accidents.
The Ford Engineering Laboratory played a vital role in this evolving landscape. In response to safety concerns and research from organizations such as the Cornell University Aeronautical Research Lab, Ford engineers began exploring and developing innovative safety concepts. Some of these included radical design elements, like swiveling front seats, aimed at minimizing the impact of accidents on vehicle occupants. While some of these concepts might seem unusual today, they demonstrate Ford's commitment to addressing safety challenges during this period.
The innovations pioneered by Ford in the 1950s, while perhaps not fully realized at the time, set the stage for future advances in safety features. These early explorations and implementations eventually paved the way for technologies like airbags and other safety elements that have become integral to modern vehicle designs. It's clear that the 1950s represented a critical period for recognizing and addressing safety concerns in automobiles. The groundwork laid then continues to impact vehicle safety practices even today.
The 1950s, while not initially a period of widespread emphasis on automotive safety, proved to be a crucial decade for the development of fundamental safety technologies. It was a time when the growing awareness of vehicle accidents sparked a gradual shift in the industry’s approach. Ford, along with other manufacturers, began exploring ways to make cars inherently safer, laying the groundwork for future advancements.
One notable early area of focus was improving a vehicle's resistance to rollovers. Engineers recognized that lowering the center of gravity in car designs could significantly reduce the risk of rollovers in sudden maneuvers, leading to improved occupant safety.
Furthermore, the need to understand collision dynamics propelled research into highway crash studies. These studies, pioneered by Ford engineers, helped in the development of crumple zones. The idea was that vehicles could be designed to absorb impact energy, ultimately reducing the severity of injuries for those inside. This concept is, of course, the basis of many of today's safety standards.
The 1950s also marked the early adoption of anthropomorphic test devices—crash test dummies—in safety testing. Ford was among the early adopters of this technology which was invaluable in understanding the impact of collisions on the human body. This research gave engineers a crucial window into how real people would experience vehicle crashes, enabling them to design safer vehicles.
The decade also witnessed the widespread adoption of safety glass. Laminated glass, unlike the conventional glass used previously, held together in the event of an impact, thus reducing the risk of injuries from shattered glass. While glass innovation had roots in Ford’s early work (as far back as the late 1920s), safety glass became more integrated during this period.
Alongside the introduction of safety glass, seat belts—though not a new concept—gained wider acceptance. Ford’s decision to make lap belts a standard feature in vehicles marked an important step towards passenger safety. It not only provided a tangible safety benefit but also raised public awareness regarding the importance of utilizing safety features in vehicles.
Meanwhile, steering wheel design was also receiving attention. The introduction of impact-absorbing steering wheels, designed to minimize driver injuries during crashes, was a pivotal step. These innovations used materials that could compress and deform on impact, thereby minimizing the forces transferred to the occupant.
The progress in braking systems during this period also reflected the rising concern over driver and passenger safety. Dual-circuit brake systems became more integrated. These systems provided a failsafe mechanism, in the event of a failure in one circuit, the other could still function, providing a much-needed backup.
Bumpers also received a redesign. Energy-absorbing bumpers, engineered to deform during a collision, became more prevalent. This approach aimed to improve a vehicle’s ability to effectively manage the transfer of energy during a collision.
Windshield design became a point of focus as well. Ford's engineers were exploring the potential for curved windshields—not only were these helpful in improving aerodynamic performance, they also provided improvements to visibility and reduced glare.
Beyond the technological advances, it was a period when public education about safety started becoming more common. Companies like Ford were starting to run campaigns to educate consumers about the importance of using the available safety features. These efforts gradually shifted the societal viewpoint toward safer driving practices, laying a foundation for the later development of driver education and awareness campaigns.
The 1950s, with its blend of technological experimentation and a burgeoning public awareness of safety, became a critical decade for paving the way for modern automotive safety features and practices. These seemingly small innovations and efforts to make driving safer were just the beginning of the evolution in automotive engineering that led to the inclusion of advanced safety features such as airbags and more sophisticated crash structures. The legacy of that initial work in the 1950s is still evident in the way we design and build vehicles today, reminding us of the continuous drive toward making cars safer for everyone.
Ford Engineering Laboratory Celebrates 100 Years A Century of Automotive Innovation - 1970s Developing Fuel Efficiency Technologies
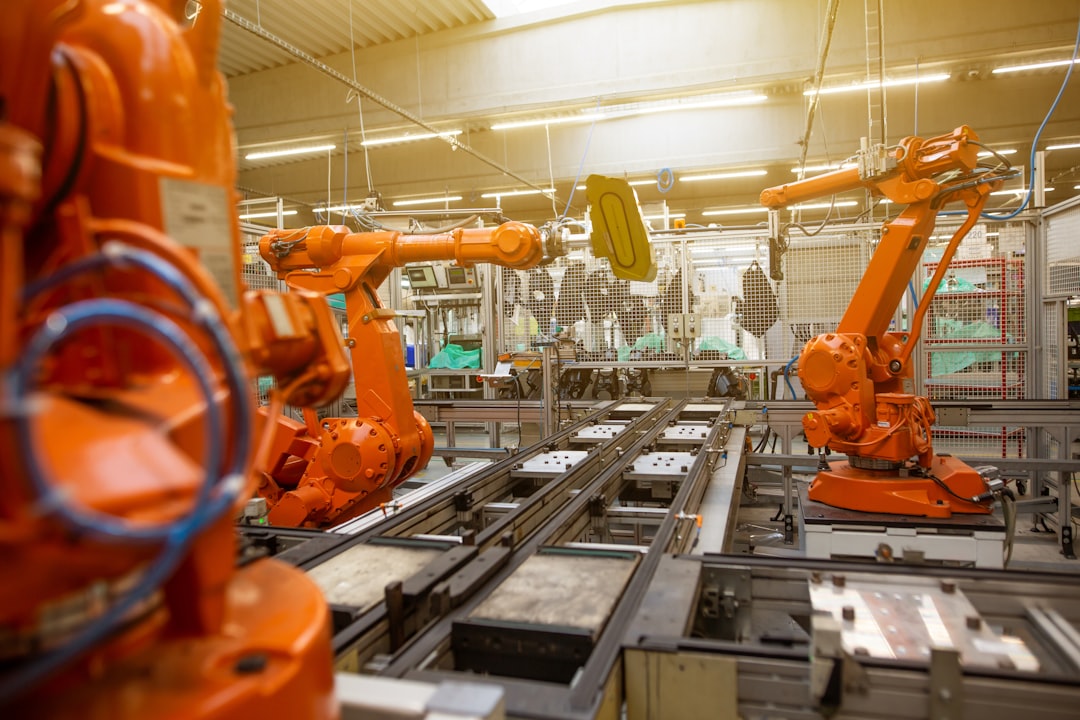
During the 1970s, the Ford Engineering Laboratory shifted its focus to developing technologies that improved fuel efficiency. This change was driven by the global oil crisis, which sent gasoline prices soaring and altered consumer preferences. The 1975 Ford F-150, launched during this period, exemplifies the shift towards vehicles that offered better fuel economy without compromising performance. This growing demand for fuel-efficient cars was further reinforced by the enactment of the Corporate Average Fuel Economy (CAFE) standards in 1975, which required automakers to improve the fuel efficiency of their vehicle fleets. Despite the difficulties presented by escalating fuel costs, Ford's engineering team responded with a wave of research and development, seeking to create engine designs and vehicle configurations that catered to this changing market. Many of the innovations explored during this decade have served as a foundation for ongoing improvements in fuel efficiency, and their legacy can still be seen in the design of vehicles today.
The 1970s presented a unique challenge and opportunity for automotive engineers—the oil crisis. Suddenly, fuel efficiency wasn't just a desirable attribute; it was a necessity. The Ford Engineering Laboratory, like other engineering centers, found itself thrust into a period of rapid innovation, forced to re-evaluate design priorities. The US Congress, reacting to the crisis, enacted the Corporate Average Fuel Economy (CAFE) standards in 1975. These regulations mandated that automakers, including Ford, achieve certain fuel efficiency targets across their entire vehicle lineup. This was a huge shift, fundamentally altering the way vehicles were designed.
The market itself was rapidly changing. Consumers, facing soaring fuel prices, began gravitating towards smaller, more fuel-efficient vehicles. The Ford Pinto, released in this era, exemplifies this shift. It's fascinating to see how consumer preferences influenced product development.
Engineers started to explore diverse strategies to improve fuel efficiency. Aerodynamics, once perhaps a minor design consideration, became a major factor. Wind tunnels emerged as invaluable tools, helping designers understand and minimize air resistance, especially on larger vehicle types. Fuel injection systems started gaining ground, offering more precise control over fuel delivery compared to older carburetor systems.
It’s also interesting how material science played a role. Lighter materials like aluminum and plastics began to be used more extensively, helping to reduce vehicle weight and therefore decrease fuel consumption. Engineers also investigated high-compression engines, exploring ways to improve fuel combustion and, in turn, MPG. It's important to note that some of these changes were driven by a combination of technological advancement and the need to meet government requirements. Electronic ignition systems, offering better combustion timing and fuel efficiency, also became widely adopted during this period.
The 1970s was a time of rapid learning and experimentation. While the concept of hybrid vehicles would be commercially developed later, the seeds of these ideas were planted in this decade. Engineers started thinking about integrating electric motors with internal combustion engines, hinting at future trends in vehicle technology. Interestingly, fuel economy became a major selling point in marketing materials, showcasing how fuel efficiency was shaping consumers’ purchasing decisions. The MPG rating went from being a technical detail to a major deciding factor in the buying process.
The oil crisis acted as a powerful catalyst for innovation in the automotive world. Engineers responded with a burst of creativity, applying new technologies and concepts to improve fuel efficiency. This era of rapid change and adaptation in vehicle development would have lasting effects on the automotive industry, laying the groundwork for many of the fuel-saving technologies we see today.
Ford Engineering Laboratory Celebrates 100 Years A Century of Automotive Innovation - 1990s Advancing Computer-Aided Design in Car Manufacturing
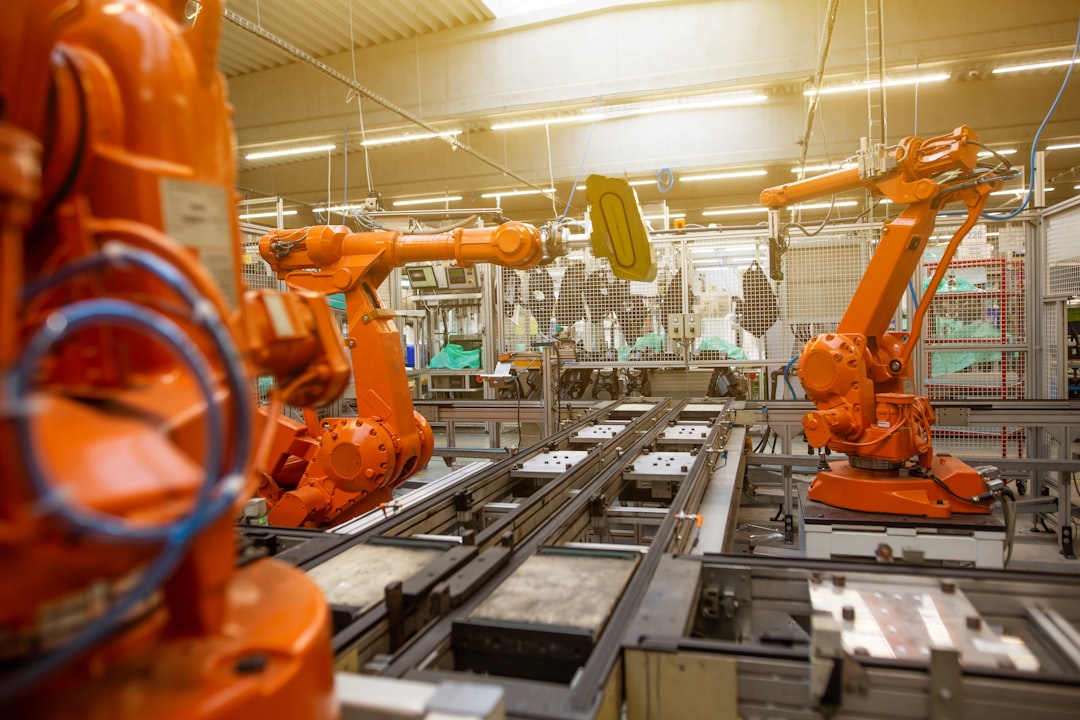
The 1990s witnessed a surge in the use of Computer-Aided Design (CAD) within car manufacturing, significantly impacting how vehicles were engineered and built at companies like Ford. This period saw a transition where CAD evolved from a supporting tool to a cornerstone of the design process, leading to enhanced design flexibility, efficient use of materials, and faster prototyping. The ability to create more elaborate designs and perform intricate simulations became a significant advantage, accelerating the development of complex vehicles like the Ford GT. Moreover, the use of CAD improved the organization and accessibility of engineering data, fostering smoother collaborations among designers and engineers.
Despite these notable improvements, the increasing intricacy of CAD software and systems introduced new challenges. The complexity of the software created questions about how these tools best integrated into existing engineering workflows and how to maintain an appropriate balance between human expertise and automated design elements. This period of innovation therefore showcased a dual nature to technological advancements, offering both profound benefits and unforeseen obstacles in the manufacturing process. The decade's innovations exemplify the continuous tension between maximizing technological opportunities and carefully managing their consequences in the world of automotive design and development.
The 1990s marked a pivotal era for car manufacturing, driven by the increasing sophistication of computer-aided design (CAD) tools. It was a time when the initial forays of CAD in the 1980s really started to mature and make a significant impact. Engineers found themselves increasingly able to create highly detailed 3D models of vehicle components, offering a level of precision that was previously unimaginable. This ability to create virtual representations led to a dramatic reduction in the time and cost of physical prototyping, which was previously a very laborious process.
A key development was the growing integration of CAD with manufacturing processes, primarily through computer-aided manufacturing (CAM). This connection facilitated a smoother transition from the design stage to the actual production of car parts. Production became more efficient and precise as designs were directly translated into manufacturing instructions, reducing errors and streamlining the workflow.
Another fascinating development in the 1990s was the emergence of virtual prototyping techniques. This ability to test and refine a design entirely within a computer environment was a game-changer. It meant that engineers could conduct extensive simulations and analyses before physically building a prototype, significantly shortening the time needed to bring new vehicle models to market.
It's quite interesting to see how CAD evolved in the 1990s. The software became more intelligent, incorporating algorithms that could suggest design adjustments based on specific performance targets. These features challenged engineers to think differently about their traditional approaches to vehicle design.
The adoption of CAD also created opportunities for collaboration on a global scale. New CAD platforms allowed teams scattered across different parts of the world to simultaneously work on the same design project. This development significantly boosted communication and streamlined the engineering process, especially for multinational car companies such as Ford, who had design and manufacturing facilities in various countries.
The application of CAD to vehicle interiors led to improvements in ergonomics. Software tools began incorporating features that could analyze human factors, helping engineers to create not just visually appealing but also comfortable and user-friendly vehicle interiors.
Finite element analysis (FEA), a technique used to predict how structures react to stress, was also gaining popularity within CAD environments. This allowed engineers to better simulate the stresses and strains on various vehicle parts in different conditions, which was essential for ensuring vehicle safety and structural integrity before subjecting physical prototypes to rigorous testing.
The 1990s also saw a rise in the use of advanced surface modeling techniques. This allowed designers to create increasingly complex and visually appealing shapes for car exteriors. The ability to precisely manipulate surfaces offered much more creative freedom, pushing the boundaries of what was considered aesthetically pleasing in vehicle designs.
However, this rapid advancement in CAD technology came with some challenges. As the complexity of CAD models grew, so did the amount of data needing to be managed. This led to issues with version control and data tracking. Automotive companies had to implement robust data management systems to effectively manage the immense datasets associated with increasingly sophisticated CAD workflows.
This widespread adoption of CAD not only streamlined the design process but also had a major influence on the supply chain. The way parts were specified and ordered changed significantly. Manufacturers were able to more accurately define the parts they needed and order them more efficiently. This optimization of the supply chain resulted in a faster overall manufacturing process from the initial design stage to final product delivery.
It's clear that the 1990s were a pivotal time for CAD in the automotive world. The increased power of these tools allowed engineers to work in ways that were previously impossible, revolutionizing the entire design-to-manufacturing process. These advancements helped pave the way for the complex and interconnected engineering and manufacturing processes used in the automotive industry today.
Ford Engineering Laboratory Celebrates 100 Years A Century of Automotive Innovation - 2010 Embracing Electric Vehicle Research
By 2010, Ford's engineering focus had shifted gears, embracing electric vehicle (EV) research as a key area of development. This reflected a broader industry trend towards sustainability and a recognition that the future of automobiles was increasingly intertwined with electrification. Ford's ambitions were clear: reimagine their entire vehicle lineup by 2030, with a commitment to entirely electric or plug-in hybrid commercial vehicles by 2024. To support these goals, they invested in a new manufacturing facility in Cologne, Germany, specifically designed for large-scale production of EVs, and launched a collaborative lab in Michigan dedicated to improving battery technology.
However, transitioning a large, established company like Ford to a primarily EV-focused manufacturer presented a significant challenge. The integration of new battery technologies, charging infrastructure, and the associated manufacturing processes required considerable adjustments within Ford's established systems. Maintaining this balance between innovative goals and the need for streamlined production proved to be a key hurdle. The era of 2010 marked a turning point, a pivotal moment where Ford acknowledged the industry's change and committed to an EV-centric future, all while grappling with the complexity of incorporating such a transformative technology into its existing framework. The challenges faced by Ford in this period represent a broader dynamic within the industry, showcasing a period of both opportunity and disruption.
By 2010, Ford's research efforts had begun to shift towards the burgeoning field of electric vehicles. This change in focus was likely driven by a confluence of factors including growing awareness of environmental concerns and the potential for innovation in propulsion technology. Early research highlighted the potential for electric motors to achieve remarkably high efficiencies—upwards of 95%—significantly outperforming traditional internal combustion engines. This efficiency advantage represented a major shift in automotive engineering, challenging the long-held assumptions about how vehicles could be powered.
The concept of regenerative braking was another area of intense investigation. This technology, which allows an electric vehicle to recapture energy typically lost during braking, held the promise of increased efficiency and longer battery life. Researchers and engineers were intrigued by the potential to improve a vehicle's overall energy efficiency, and this concept was poised to become a key component in the development of more practical electric vehicles.
The 2010s also saw notable advancements in lithium-ion battery technology. Energy density, a measure of how much energy a battery can store in a given space, increased significantly. This meant that battery packs could store more energy in a smaller and lighter form, leading to greater driving ranges and potentially alleviating the 'range anxiety' that was a common barrier to the adoption of EVs. This technological leap was crucial for making electric vehicles more practical and compelling for consumers.
The availability of charging infrastructure was another crucial factor during this period. It is likely that the expanding number of publicly accessible charging stations, fueled by both market demand and government support, also contributed to the growing interest in electric vehicles. While charging infrastructure expansion was still in its early stages, it was evident that wider availability was a crucial element for broader consumer adoption.
The overall economics of electric vehicles were also undergoing change. The price of producing lithium-ion batteries, a major factor in the overall cost of an EV, had been steadily declining. Although the production cost for these batteries was still substantial in 2010, there was clear potential for continued price reductions. Such a decline would have been a significant factor in driving broader market adoption.
The expanding global EV market in 2010, with some notable production increases in countries like China and the United States, demonstrated a growing recognition of EVs as a potential replacement for traditional vehicles. The diversification of the market and increase in manufacturing suggested that the field had shifted from an academic curiosity to a serious business proposition.
Early research also looked into how electric vehicles could be integrated with smart grid technologies. The possibility of using EVs as energy storage units, charging and discharging in response to changes in electricity demand, was being considered. This was a novel idea with potential for broader implications for energy distribution and management.
Aerodynamic design was also gaining increased attention as a way to improve the efficiency of EVs. Studies that showed significant efficiency gains from reducing drag—as much as 20%—highlighted the importance of aerodynamic design for the future of EVs. Engineers and designers were probably seeking innovative ways to create vehicles that could slip through the air with minimal resistance, maximizing energy efficiency.
In 2010, engineers and researchers were actively seeking to reduce the weight of vehicles through the use of lighter-weight materials. This research included exploration of advanced materials such as carbon fiber and aluminum composites. The aim was to optimize energy usage and improve vehicle performance, a significant development area that could have far-reaching implications for both EV efficiency and overall performance.
Heat management became an important area of research, too. The challenges associated with managing the heat generated by electric vehicle components, particularly within the battery packs, required the development of specialized cooling systems. This research area was essential for ensuring the long-term reliability and safety of electric vehicle components.
The beginning of the 2010s marked a period of growing interest in electric vehicle technology. Researchers and engineers explored a range of key concepts and areas of innovation that were destined to shape the development of electric vehicles. These early research efforts were essential in laying the foundation for the rapidly expanding electric vehicle market that we see today.
Ford Engineering Laboratory Celebrates 100 Years A Century of Automotive Innovation - 2024 Looking Ahead Ford's Next Century of Innovation
Standing at the threshold of its second century in 2024, Ford's innovation efforts are increasingly centered on responding to shifting consumer desires and bolstering its technological prowess. Recent insights indicate a noteworthy cultural trend where a sizable portion of the workforce is prepared to accept reduced earnings for a lifestyle they value more. In reaction, Ford is stepping up its focus on electric and interconnected vehicles, introducing initiatives like the Atlanta Research and Innovation Center. This transformative drive mirrors a larger industry movement towards sustainability and technological advancement, especially concerning electric vehicles and clever solutions for mobility. Ford's overall strategy seeks to harmonize its historical successes with the pressing necessity for continuous innovation in a swiftly evolving auto industry. It will be interesting to see if these new directions truly address the evolving demands and if the company can manage a seamless transition. There's an inherent risk in such a drastic change, especially in a traditionally conservative sector like the auto industry.
Looking ahead to 2024, Ford's engineering efforts are focused on a diverse range of initiatives aimed at shaping the next century of automotive innovation. While the push toward electrification remains a core aspect of their strategy, there's a growing emphasis on bolstering the resilience of manufacturing operations. The recent disruptions caused by various global events have pushed Ford to invest in advanced robotics and AI-powered analytics. This investment enables their factories to adapt more readily to changing demands, adjusting output on the fly to meet fluctuations in customer needs and market shifts. This ability to quickly respond is vital in the current complex environment.
Autonomous vehicle technology is another key area for Ford's engineering team. Integrating machine learning into autonomous vehicle systems allows them to refine sensor technology, ultimately leading to improved environmental perception, potentially enhancing the safety and operational efficiency of self-driving vehicles. However, some challenges persist with this technology. The integration of such sophisticated systems requires rigorous testing and validation to ensure both safety and reliability.
It's interesting to observe how Ford is branching out beyond traditional automotive collaborations. Partnerships with leading software companies are speeding up the integration of cloud computing into vehicle systems. This type of integration leads to enhanced data management capabilities within vehicles and also enables real-time diagnostics, helping to pinpoint and troubleshoot issues quickly. However, the reliance on remote computing resources introduces vulnerabilities that require careful consideration and robust cybersecurity protocols.
Augmented reality (AR) has emerged as another tool in Ford's engineering toolbox. Ford engineers are utilizing AR in both design and repair contexts. The idea is to provide technicians with heads-up displays that overlay important information directly onto vehicle components. This feature should help reduce mistakes and improve the efficiency of both vehicle assembly and maintenance operations. The long-term implications of integrating AR are still somewhat uncertain, but the technology holds immense potential to enhance overall operational efficiency.
While battery electric vehicles (BEVs) remain a key element of Ford's strategy, the company hasn't abandoned alternative technologies. Their research for 2024 includes significant advancements in hydrogen fuel cell technology. Testing has revealed that under certain conditions, hydrogen fuel cells can offer advantages over BEVs, including faster refueling times and longer ranges. This area has attracted considerable research across industries but its successful commercial implementation for automobiles is still a challenge.
Furthermore, Ford has been significantly investing in advanced simulation technologies. This enables their engineers to perform complex simulations including collision dynamics and structural integrity tests before physical prototypes are even built. This investment should reduce development time and expenses, but the tradeoff is that simulations are not a perfect substitute for real-world testing, especially when it comes to safety-related features.
3D printing is another manufacturing trend that Ford has embraced. Ford is integrating this into their design and engineering processes. Using 3D printing for prototyping and parts production allows for faster turnaround times and potentially improves overall efficiency and waste reduction. However, scaling up 3D printing for large-scale production might prove challenging, especially in meeting the cost and quality expectations of traditional manufacturing methods.
Materials science also remains a key area of focus. Ford is actively investigating materials such as graphene and other advanced composites. These materials exhibit enhanced strength-to-weight ratios, promising significant reductions in overall vehicle weight. But adopting these materials in a cost-effective manner is a significant hurdle that needs to be addressed for broader integration.
Ford has also developed a system that leverages the Internet of Things (IoT) to collect real-time feedback from connected vehicles. This continuous flow of data will aid in ongoing vehicle improvements and can be used to develop predictive maintenance practices, enabling proactive service and potentially preventing breakdowns. However, the enormous volume of data generated by these connected systems will need to be effectively managed, introducing complexities into data storage, analysis, and security protocols.
As a corollary, Ford's engineers are prioritizing cybersecurity in their vehicle designs. Connected vehicles open up a new class of vulnerabilities and potential attack surfaces. The company has introduced new, more stringent security protocols to help protect their vehicle systems from hacking. However, the ever-evolving nature of cybersecurity threats requires ongoing vigilance and adaptation of defense strategies.
Overall, Ford's engineering agenda for 2024 demonstrates a company deeply engaged in the ongoing revolution within the automotive industry. This drive to innovate reflects both a strategic response to broader industry shifts and a recognition that continuous technological development is a prerequisite to success in this dynamic sector. However, it's clear that these new technologies introduce novel complexities in manufacturing, reliability, safety, and cybersecurity—challenges that Ford will have to continuously adapt to and address moving forward.
More Posts from agustin-otegui.com: