Concrete Prices Expected to Stabilize in Late 2024 Despite Early Year Increases
Concrete Prices Expected to Stabilize in Late 2024 Despite Early Year Increases - Early 2024 price hikes due to ongoing supply chain challenges
The start of 2024 is expected to see a surge in the cost of construction materials, primarily due to the lingering effects of supply chain disruptions. While concrete prices briefly dipped late last year, they're now on the rise, a symptom of these ongoing challenges. The situation is worsened by the continuing labor shortages, which add to the pressure on costs, even as overall inflation appears to be moderating. Furthermore, shipping delays—some related to international conflicts—are creating added uncertainty and potentially pushing material prices higher. Despite these headwinds, experts predict that prices for construction materials will ultimately settle down towards the end of 2024, though we can expect fluctuations in the early months.
Following a period of relative stability in late 2023, the early months of 2024 have witnessed a resurgence in concrete price increases, particularly in certain areas, with some experiencing a notable 15% jump. This upward trend appears to be strongly tied to lingering global supply chain issues, a consequence of ongoing international events. The difficulties in securing both the raw materials needed for concrete, like cement and aggregates, and transporting them efficiently have intensified, causing a shortage and subsequently inflated prices.
Beyond the immediate material shortages, the construction industry continues to grapple with a labor shortage, which in turn is pushing wages higher. This adds another layer to the rising costs of concrete production and installation. While some efforts are being made to innovate and improve logistics – like using data analytics to refine inventory management – implementing these changes takes time due to their complexity.
It’s also noteworthy that the demand for concrete has increased due to competition from other industries, especially within the broader construction materials sector. This heightened competition has spurred bidding wars for the limited available resources. Indirectly, environmental regulations are starting to play a role, limiting the sources of certain materials needed for concrete production and affecting pricing patterns.
Examining past global crises and their impact on supply chains suggests that these disruptions can stretch for well over a year. This raises the prospect that we may see extended periods of higher prices for concrete before a stabilization in the market. The push to use recycled materials in concrete production has gained some traction, but the costs involved in processing these materials and the limited availability of suitable recycled aggregates are significant hurdles to broader adoption.
The continued volatility in international shipping, particularly for imported components, continues to create uncertainty. Shipping fees, during times of heightened disruption, can amount to a significant portion – up to 25% – of the overall material cost. As a final observation, various companies are exploring the use of autonomous delivery systems, such as drone delivery for smaller concrete components, to improve efficiency and mitigate some of the ongoing logistical challenges. The ultimate impact of these novel solutions remains to be seen.
Concrete Prices Expected to Stabilize in Late 2024 Despite Early Year Increases - Labor shortages drive up concrete finishing costs by 85%
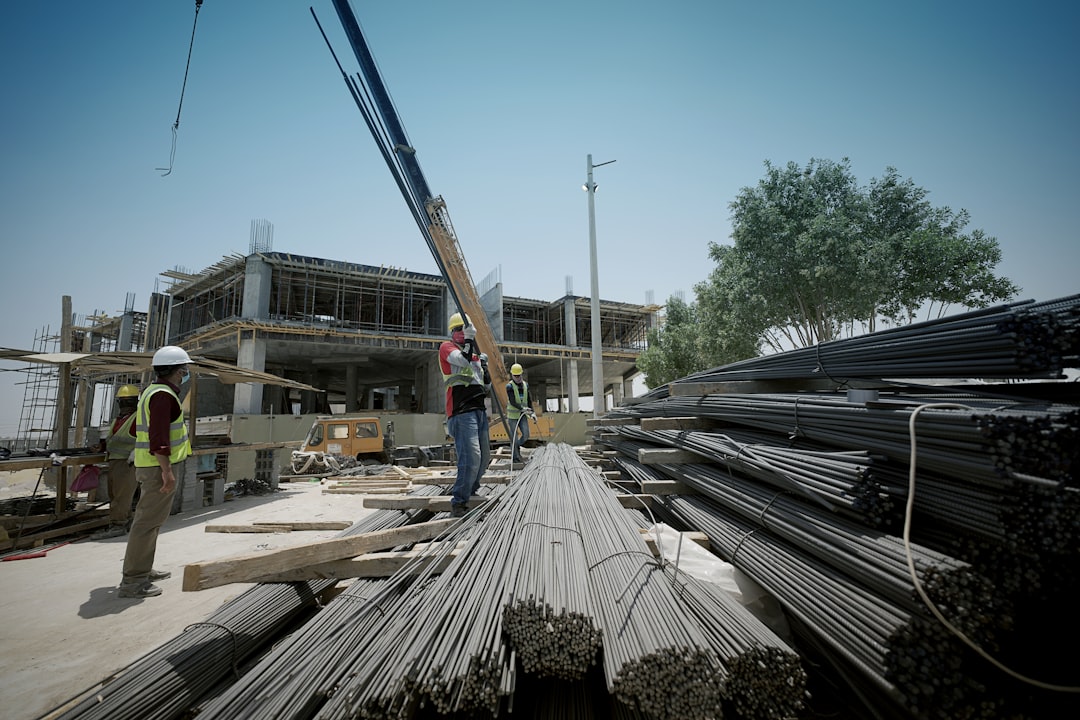
The ongoing shortage of skilled labor is having a significant impact on the cost of finishing concrete, with reports showing an 85% increase in some areas. This surge in costs is occurring despite a general softening of construction expenses, primarily due to a drop in material prices. However, the construction sector continues to battle a persistent lack of skilled workers, which is pushing labor costs higher. As demand for concrete remains strong, the increased need for skilled labor and higher wages are further pushing up costs and creating a more challenging environment for concrete projects.
Experts in the field believe that these labor shortages will likely persist, indicating that this cost pressure is unlikely to ease soon. While the price of certain materials might start to decrease, labor-related expenses are a considerable barrier to any significant stabilization in concrete prices. This highlights that while the broader market may be heading towards more stability, labor cost pressures represent a significant challenge that could prolong the period of higher overall costs in the concrete market.
The persistent shortage of skilled labor has significantly impacted the cost of concrete finishing, with some areas experiencing a staggering 85% increase in labor costs. This surge is a direct result of the difficulty contractors face in finding qualified workers, leading to higher wages and extended project durations. The nature of concrete finishing – requiring specialized skills in smoothing, leveling, and curing – makes it particularly sensitive to labor availability, magnifying the impact of even small workforce fluctuations.
The problem stems from several interconnected factors. A notable trend is the aging workforce in the construction sector, with a significant portion of the existing labor pool nearing retirement. The pipeline of young people entering trades isn't keeping pace, creating a significant gap in skilled labor, especially for concrete finishing. This demographic shift contributes to the financial pressures builders face.
It's also important to recognize that this labor shortage isn't exclusive to the concrete sector, but a broader issue across industries. It signifies a systemic risk to infrastructure and housing development if it continues to worsen. Beyond financial impacts, it's crucial to acknowledge that labor shortages may contribute to reduced safety on construction sites. With a diminished pool of skilled workers, projects might rely on less experienced individuals, potentially increasing the risk of accidents and associated delays and liabilities.
While technological solutions, like automated finishing machines, offer a potential avenue for mitigating the labor burden, their widespread adoption is hindered by substantial upfront investment costs, especially for smaller contractors already burdened by rising prices. This situation has some companies exploring ways to cut project costs by focusing on efficiency – sometimes sacrificing quality or scope – raising concerns about long-term infrastructure reliability.
The current labor shortage has also triggered a reaction from educational institutions and businesses, who are investing more heavily in training programs for the next generation of concrete finishers. However, the full impact of these efforts on the market hasn't yet materialized. Further, local governments in some areas are evaluating policies to encourage apprenticeships or workforce development, suggesting a possible shift in how the industry manages labor dynamics. The effectiveness and long-term implications of such policies are yet to be determined, but they demonstrate a growing awareness of the urgent need for solutions.
Concrete Prices Expected to Stabilize in Late 2024 Despite Early Year Increases - Q4 2023 saw 5% quarterly increase in construction material costs
During the final quarter of 2023, the cost of construction materials saw a 5% jump compared to the previous quarter. This upward trend, which has been gaining momentum since 2021, is a direct consequence of the lingering effects of supply chain disruptions and labor shortages. While the early part of 2024 has seen a slight overall decrease in construction costs, driven largely by falling material prices, volatility in material costs remains. This creates uncertainties in budgeting and project scheduling, especially for projects heavily reliant on materials. These rising costs have substantial implications for concrete prices, adding to the complexity of the market outlook. Even with forecasts predicting some stabilization in late 2024, the interplay of fluctuating material prices and persistent labor challenges creates obstacles that might extend the period of higher costs.
Looking back at the latter part of 2023, we see a 5% increase in construction material costs during the fourth quarter. This jump adds to the ongoing trend of rising material costs that began in 2021, accelerating later in 2022. Although this increase was below the peak levels of 2022, it still points to a continued period of instability and volatility within the construction materials sector.
Interestingly, while material costs overall dipped slightly between the third quarter of 2023 and the first quarter of 2024, a 1.25% decrease, this was primarily driven by a 3.5% drop in material prices. During this same time, labor costs rose by 2.7%, a reflection of the ongoing skilled labor shortage. It's curious how these two aspects – materials and labor – are pulling in opposite directions.
The expectation is that concrete prices, which have seen some early 2024 increases, will level off and potentially decrease by 1% to 2% annually through 2025. However, it's a mixed bag, as other materials, such as plastics, wood, and plaster composites, are expected to see annual price increases of up to 6.5%. This creates a bit of a puzzle in terms of how these different material cost trends will interact in the coming months.
Looking at the bigger picture, construction costs nationwide rose roughly 15.3% in the year ending Q4 2023. This highlights the overall inflationary pressure impacting the industry. Meanwhile, domestic trucking costs have been decreasing, potentially easing pressure on transportation costs for some materials.
Recent data from industry reports indicates that, despite the initial increases in 2024, construction material costs might eventually trend downwards in the remainder of the year. It will be interesting to observe how these various cost pressures impact the final pricing of construction projects and whether the predicted stabilization in concrete prices will indeed occur. It appears that while material costs are showing some signs of settling, labor costs continue to be a hurdle for stabilizing prices across the board. There's a lot to consider when evaluating the long-term future of construction costs, and it's a complex picture.
Concrete Prices Expected to Stabilize in Late 2024 Despite Early Year Increases - Steel mill products show 1% price decline in 2023
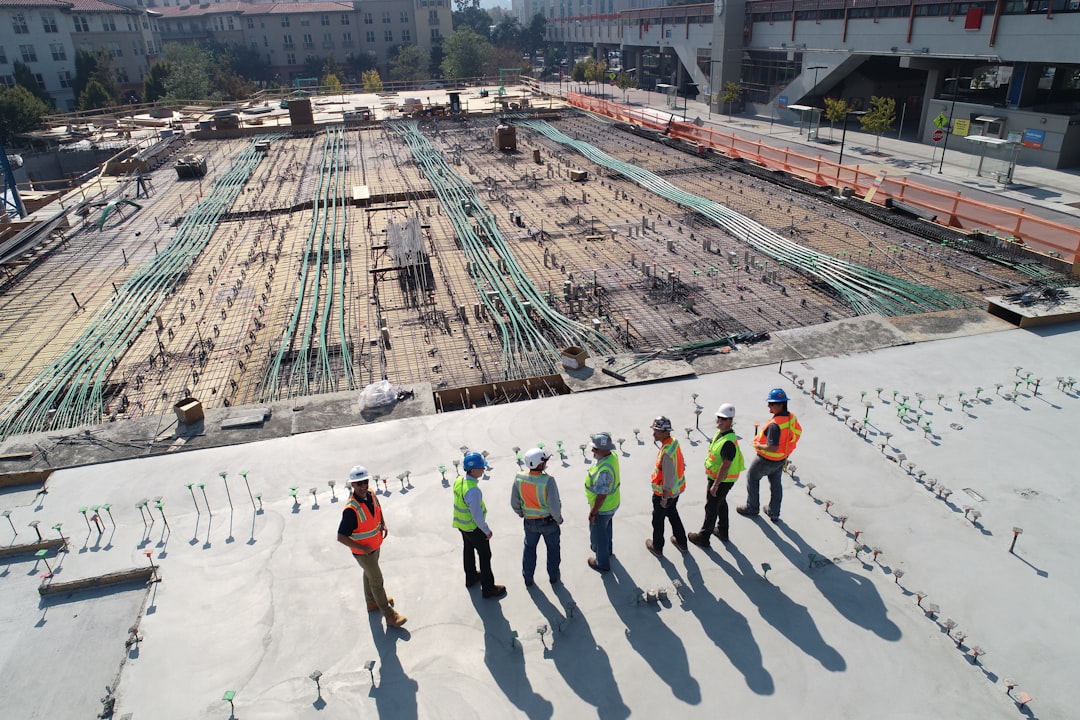
Steel mill product prices dipped slightly in 2023, falling by about 1%, a change after a period of significant price increases in the preceding years. This decline is notable, given that steel prices had risen considerably in 2021 and 2022. While steel prices did see a small uptick in December of 2023, the overall trend remains downward, with prices now considerably below their peak, down by around 31%. This movement in steel prices presents an interesting contrast to the upward trajectory of concrete prices, which saw a substantial increase in 2023. The ongoing challenges related to supply chain interruptions and the scarcity of skilled labor continue to create uncertainty and volatility in construction material costs, making project planning and budgeting a tricky process. Given the fluctuations in overall construction costs, the impact of steel's recent price changes will be an important factor to consider when evaluating the overall dynamics of the building materials market.
The 1% decrease in steel mill product prices during 2023 stands out against the broader trend of rising construction material costs. This unexpected dip could be a sign of softening demand, which is intriguing given the ongoing inflation in the construction sector. It suggests that the market for steel might be reacting differently to economic pressures compared to other construction materials like concrete, which experienced price increases in the same period.
This divergence in price movements between steel and concrete is notable. It highlights the complex interplay of factors impacting different construction materials. For example, the steel market's response might reflect broader shifts in supply chain dynamics, where fluctuations in one sector can influence others. Changes in steel production might not directly impact concrete prices, but they could certainly cause unpredictable ripple effects on construction project budgets.
Furthermore, the impact of this steel price decline may not be uniform geographically. Some areas could see more pronounced reductions due to localized oversupply or decreased demand. These regional differences could further complicate logistics and pricing strategies for construction companies. It is interesting to consider how variations in steel pricing could lead to complex challenges in procuring and transporting materials efficiently.
Moreover, despite the reduced prices, the costs of producing steel haven't decreased proportionally. This is partly due to the persistent challenges of labor and energy expenses, which manufacturers must navigate. It indicates that the price reduction may be driven by a decrease in revenue rather than a decrease in production costs, which is concerning for the long-term health of the industry.
The global economic landscape also influences steel demand. Many countries are currently dealing with economic slowdowns, which could be contributing to the lower steel prices. This suggests that the international economic climate plays a larger role than anticipated in determining the price of steel.
The 1% decline might also reflect a cautious approach among builders and developers. They may be anticipating further cost and availability fluctuations in the future, influencing their procurement decisions. Such uncertainty can lead to more cautious strategies when ordering materials, causing a delay in large projects.
Technological improvements in steel production could also be a factor. While efficiency gains can lead to cost reductions, they also create uncertainty in the market by changing dynamics in unpredictable ways. The industry's innovations and their potential impact on project timelines and cost estimations warrants further investigation.
The role of international trade policies shouldn't be underestimated either. Global trade tensions and tariffs on steel imports can significantly influence domestic prices. This creates a complex environment for companies, as they adjust to changing costs influenced by geopolitical factors instead of the intrinsic value of steel.
Looking ahead, the future of steel pricing remains uncertain. Analysts believe that, while prices have dipped, there could be further volatility due to factors like expanded domestic capacity and international trade dynamics. This reinforces the need for careful forecasting of steel and related material costs for future construction projects, particularly for those involving concrete elements.
Overall, the 1% decline in steel prices in 2023 presents an interesting puzzle within the construction materials landscape. It reveals a dynamic interplay of factors—ranging from global economics to domestic manufacturing and technological innovation—that shapes the cost of materials and challenges conventional wisdom about how materials should respond to market conditions.
Concrete Prices Expected to Stabilize in Late 2024 Despite Early Year Increases - Construction costs decrease 25% from Q3 2023 to Q1 2024
Construction costs saw a substantial 25% decline between the third quarter of 2023 and the first quarter of 2024. This reduction is primarily attributed to a significant 35% decrease in the cost of construction materials. However, it's important to note that the labor market remains tight, with labor costs experiencing a 2.7% increase during the same period due to persistent skilled worker shortages. This creates a mixed picture where overall construction costs are falling but specific components are experiencing upward pressure. For example, the price of concrete blocks rose 6.16% in the first quarter of 2024, hitting a three-year high. Despite these ongoing fluctuations, predictions point to a potential leveling off of material costs by late 2024, although the early months of the year are anticipated to continue the trend of volatile material pricing. Construction professionals will have to navigate these fluctuating costs to manage project budgets and schedules effectively.
The 25% reduction in construction costs between the third quarter of 2023 and the first quarter of 2024 stands out against the broader backdrop of rising prices across the construction sector. This drop hints at a potential shift in market forces, possibly related to adjustments in supply and demand. It's interesting to observe this decline, given the ongoing pressures on construction costs from other factors.
The main driver behind this decrease appears to be falling material prices. This suggests that some of the supply chain bottlenecks that have been plaguing the industry might be easing, even though labor shortages continue to be a concern. It's noteworthy that this material cost reduction has occurred despite the labor pressures, creating an intriguing situation in the market.
However, the 25% reduction could also be a temporary phenomenon. It's plausible that the decrease is related to slower construction activity during the off-season, leading to more competitive bidding and subsequently lower prices. Understanding the seasonality of construction is crucial when interpreting these data points.
The relationship between labor and material costs is complex. While material costs declined significantly, labor costs have increased, reflecting the persisting skilled worker shortage. This raises the question of how sustainable these lower construction costs will be if labor costs continue to climb, creating a potential constraint on overall cost reduction.
Historically, large swings in construction costs have often been linked to broader political and economic shifts. This leads us to consider whether this cost decrease is solely market-driven or potentially tied to changes in the global geopolitical environment that influence trade and production capabilities. It's a valuable avenue for further investigation.
This significant drop in costs presents a new challenge for construction firms needing to adjust their budgeting and forecasting strategies. Firms now face the difficult task of navigating volatile material prices while simultaneously managing increases in labor expenses. This balancing act will likely influence project timelines and profitability, presenting a challenge for the construction sector.
Furthermore, the interplay between different material prices – where some, like concrete, are experiencing increases while others are declining dramatically – reveals the intricate web of supply chain dependencies. The varied responses of different material markets to changing circumstances are worth considering when anticipating future shifts in construction costs.
It's conceivable that this decrease in overall costs might intensify competition within the construction sector, with some firms potentially lowering bids to secure contracts. This could lead to a situation where firms erode their profit margins and, perhaps more worrisome, potentially sacrifice quality and reliability in pursuit of winning contracts.
The construction industry is also seeing an uptick in logistics solutions and innovations that might contribute to maintaining lower material costs. Whether these efforts can sustain the cost reductions remains to be seen, given the constantly fluctuating nature of demand within the sector.
Ultimately, the stability of the construction market is contingent on not just the cost of materials, but also on the availability of skilled labor and broader economic conditions. Continued monitoring of these cost fluctuations is essential to fully understand whether this recent price decrease marks a true market correction or is a temporary blip. Any disruption to these factors could quickly undo recent gains.
Concrete Prices Expected to Stabilize in Late 2024 Despite Early Year Increases - Industry experts predict 3% growth rate for concrete prices in 2024
Industry experts foresee a 3% increase in concrete prices throughout 2024. This follows a period of substantial price jumps, with 2023 alone witnessing a 112% rise. While the prediction hints at some stabilization in the latter part of the year, the early months of 2024 are likely to see continued price pressure due to the persistent impact of supply chain issues and labor shortages. It's important to note that the construction industry, currently facing volatile material costs and escalating labor expenses, remains uncertain about the long-term implications of this projected stabilization. The overall picture is further complexified by the varied trends in prices of other construction materials, revealing the interconnectedness of costs within the broader market.
Industry analysts are forecasting a 3% increase in concrete prices throughout 2024. While this rate seems relatively low compared to the dramatic price swings seen in recent years, it does suggest that the market hasn't fully stabilized. It's interesting to consider that this projection comes after a period of significant price hikes and a broader construction materials market that is still facing instability.
Considering the historical average concrete price increase of roughly 2-3% before the pandemic, this 3% growth estimate for 2024 might indicate a lingering impact from supply chain and labor challenges. However, it's also notable that various factors, like changes in energy costs, can influence the price of concrete production. Cement production, for example, is highly energy-intensive, making it sensitive to fluctuations in energy markets, especially natural gas.
Additionally, concrete prices are often intertwined with the cost of other materials, like steel. A past pattern shows that a 10% increase in steel prices can correlate with a roughly 3% rise in concrete prices. This suggests that ongoing developments in the steel sector could influence concrete's price trajectory. The recent fluctuations in steel prices, even with a slight overall decline, are a reminder that changes in related sectors can cause ripple effects throughout the construction industry.
Furthermore, labor shortages continue to play a significant role in the cost of concrete, especially finishing work. In some regions, highly skilled concrete finishers are now earning over $30 per hour, driving up labor costs even as some material prices might be moderating. The interplay between these opposing forces – materials potentially trending down and labor costs rising – creates an interesting dynamic within the market.
The concrete market is also subject to geographical factors. Some states or regions experiencing intense construction activity may encounter much higher price increases, potentially exceeding 10%. Conversely, areas with more subdued construction activity might not see the same level of price pressure. This reinforces the point that local demand and supply conditions can be a powerful force in influencing prices.
It's also worth noting the impact of automation within the industry. While there are long-term prospects for reducing production costs with robotics and automation in concrete plants, the initial implementation costs can be substantial and might lead to temporary price spikes. This situation could create a short-term increase in concrete prices before potential cost savings are realized over time.
All of these factors paint a complicated picture for the future of concrete pricing. While the 3% growth estimate seems relatively modest, it does suggest that the sector is still navigating the challenges arising from recent volatility and the broader economic environment. It will be worthwhile to continue monitoring the factors driving these price shifts to see if the projected stabilization in late 2024 becomes a reality.
More Posts from agustin-otegui.com: