Arrival's Microfactory Model Revolutionizing Electric Vehicle Production in 2024
Arrival's Microfactory Model Revolutionizing Electric Vehicle Production in 2024 - Arrival's Bicester Microfactory Completes First Production Verification Van
Arrival's Bicester microfactory has taken a notable step forward with the completion of its initial production verification van. This prototype van isn't destined for the market; instead, it will be rigorously tested and evaluated to fine-tune production quality. The microfactory, employing cutting-edge technologies like composite materials and automated robots, is presented as a template for a more efficient and adaptable approach to electric vehicle construction. This achievement signifies Arrival's progress in scaling up production, with the ultimate goal of delivering vehicles to customers sometime soon. It remains to be seen if this novel microfactory model can truly alter established norms within the automotive manufacturing sector.
Arrival's Bicester facility has recently taken a step forward in its quest to revolutionize EV manufacturing by completing its first production verification van. This van, built within the microfactory environment, won't be headed to a customer just yet. Instead, it will be subject to rigorous testing and validation procedures to ensure it meets quality standards. It's interesting to see how the facility's integrated software and in-house robotic systems have contributed to this first output. The design and construction, incorporating composite materials and autonomous robots, are a core part of Arrival's innovative approach.
This marks a tangible progression in their microfactory concept, demonstrating its capacity to produce functional vehicles. It's a good indication that their strategy of using flexible cell architectures and a software-defined manufacturing environment might be workable at scale. Of course, the real test lies ahead, as the microfactory strives to ramp up production to its intended output level. The future success of this endeavor, which has backing from entities like UPS and Hyundai, hinges on their ability to further refine the process and deliver a steady stream of EVs that meet market demands. It remains to be seen whether the microfactory model, designed for agility and localized production, will ultimately be the game-changer they envision in the EV industry.
Arrival's Microfactory Model Revolutionizing Electric Vehicle Production in 2024 - South Carolina Microfactory Shifts Focus to Electric Bus Production
Arrival's South Carolina microfactory, initially envisioned as a more versatile production hub, is now primarily geared towards building electric buses. This shift in focus is part of Arrival's broader plan to utilize a cell-based assembly system, which offers flexibility in manufacturing different vehicle types. The $46 million investment into the facility, located in York County, is meant to support a local supply chain by prioritizing components and materials from the surrounding area. While the growing interest in electric buses for public transportation may make this a logical move, concerns arise regarding the long-term viability of specializing in a single vehicle segment. Given the rapid pace of innovation and evolving demands within the wider electric vehicle market, Arrival must ensure its South Carolina microfactory remains nimble and adaptable to stay competitive. Ultimately, the success of this venture hinges on Arrival's capacity to navigate the challenges of a dynamic industry and achieve both innovation and efficient production.
Arrival's decision to focus their first US microfactory, situated in South Carolina, on electric bus production seems like a strategic move. The demand for electric buses is rising as public transit systems globally explore alternatives to traditional diesel models. Electric buses promise reduced maintenance costs because of their simpler mechanical design, making them an attractive option.
This South Carolina microfactory showcases Arrival's unique modular design philosophy. This approach allows for a very flexible production setup, which means they can potentially shift from building one type of vehicle to another quickly and efficiently. This could be crucial for maximizing productivity as demand shifts. The factory makes heavy use of automation, with robots programmed using machine learning. These sophisticated systems should enhance precision and minimize the impact of human error during assembly.
The use of composite materials is interesting from a material science perspective. Not only do these materials potentially reduce the weight of the buses, improving efficiency, but they also seem to offer better durability. This could lead to longer-lasting buses and possibly lower overall lifetime costs.
The microfactory concept itself seems geared towards efficiency. The design takes up a smaller space than traditional factories, and the just-in-time inventory system is a cost-saving feature that's quite common in manufacturing. The South Carolina plant can build buses equipped with various smart technologies, including the ability to monitor themselves and report data. This could be really helpful for predictive maintenance and minimizing downtime in the bus system.
Another notable aspect is Arrival's focus on producing the battery packs within the microfactory. This approach should enhance quality control and enable a tighter integration of the battery within the overall design of the bus. This could be key in optimizing weight and space utilization within the bus.
The microfactory is built to be easily expandable. As demand grows, they can simply add more modules, rather than needing to build an entirely new plant, which can be a major advantage over more traditional manufacturing setups. Furthermore, the use of a closed-loop manufacturing system is an environmentally responsible approach that also has economic benefits. It's a good way to control materials and costs throughout the production cycle.
Finally, the choice to establish this microfactory in South Carolina aligns with a broader US trend. We're seeing more production moving back into the US, driven by technological advancements and a desire for greater independence from global supply chains. These supply chains have proved susceptible to disruptions in recent times. While this trend can be beneficial, there are also considerations around economic and ecological impact to be considered in relation to the new localised production models.
Arrival's Microfactory Model Revolutionizing Electric Vehicle Production in 2024 - Cell-Based Assembly Method Enables Flexible Vehicle Manufacturing
Arrival's microfactory approach utilizes a novel "cell-based" assembly method that fundamentally alters the way vehicles are built. This method involves creating modular, independent assembly cells, allowing for a more flexible production process. This flexibility enables faster adjustments to shifting market demand and simpler transitions between manufacturing different vehicle models within the same facility. By integrating these assembly cells directly into existing commercial spaces, Arrival's microfactories sidestep the need for extensive and costly factory construction. This can lead to faster factory deployment and potentially lower operational costs, which could become increasingly important as the electric vehicle landscape continues to develop. While this strategy offers advantages in agility and potentially lower costs, it's still to be seen how effectively it can scale to meet larger production demands and adapt to the ongoing evolution of the EV industry. The cell-based assembly approach has the potential to significantly influence the manufacturing of electric vehicles in the future, fostering a more nimble and potentially more cost-effective manufacturing environment.
Arrival's approach to vehicle manufacturing centers around a concept called "cell-based assembly". This involves breaking down the production process into smaller, independent units or cells, each focused on a specific task. This modular approach allows them to create flexible manufacturing lines, able to shift gears more easily between different vehicle models, unlike traditional automotive factories that are often designed for just one. This shift in approach offers greater adaptability when customer demand changes, which can potentially lead to better cost management as well, by preventing scenarios of overproduction or underproduction.
One interesting implication of this cell-based setup is the ability to rapidly create prototypes for new vehicle configurations. Engineers can easily reconfigure or test variations in design much quicker than in a conventional factory, leading to faster iterative improvement of both the vehicles themselves and the production processes. They've incorporated advanced robotics, particularly collaborative robots (cobots) that are intended to assist human workers, rather than fully automate. These cobots can help with repetitive tasks, boosting overall efficiency and potentially leading to higher precision in assembly.
Since each production cell can be designed for a specific task, it allows Arrival to potentially customize vehicle builds to a much higher degree than large-scale assembly lines typically allow. The idea is that they could configure the assembly to customer orders, offering greater personalization and satisfaction. Their microfactory concept also integrates advanced software that provides real-time feedback on production performance. This ability to constantly monitor and tweak processes can be a powerful tool for spotting issues, identifying bottlenecks, and generally optimizing the manufacturing flow.
The microfactory design also appears to be a way to achieve better cost control compared to traditional factories. A reduced footprint means needing less physical space, therefore resulting in a lower initial investment. Moreover, since they're focused on sourcing components locally wherever possible, it reduces reliance on extended and potentially fragile global supply chains, resulting in faster delivery times and likely minimizing disruption risk from shortages. A notable aspect is that cell-based assembly may allow for smaller production runs to be profitable, which could encourage the exploration of more diverse and niche vehicle types.
One of the most intriguing aspects is the potential scalability of the microfactory model. Should production volumes increase, Arrival can simply add more cells to the factory as opposed to requiring a massive new building project, making expansions potentially much faster and more cost-effective. While it's still early days for this concept in the EV industry, it seems like Arrival is pursuing a path that prioritizes flexibility, responsiveness, and affordability in manufacturing. Whether this novel approach will disrupt the traditional model remains to be seen, however, in the rapidly evolving EV sector it is worth keeping a close eye on Arrival's microfactory evolution.
Arrival's Microfactory Model Revolutionizing Electric Vehicle Production in 2024 - In-House Technologies Drive Microfactory Efficiency
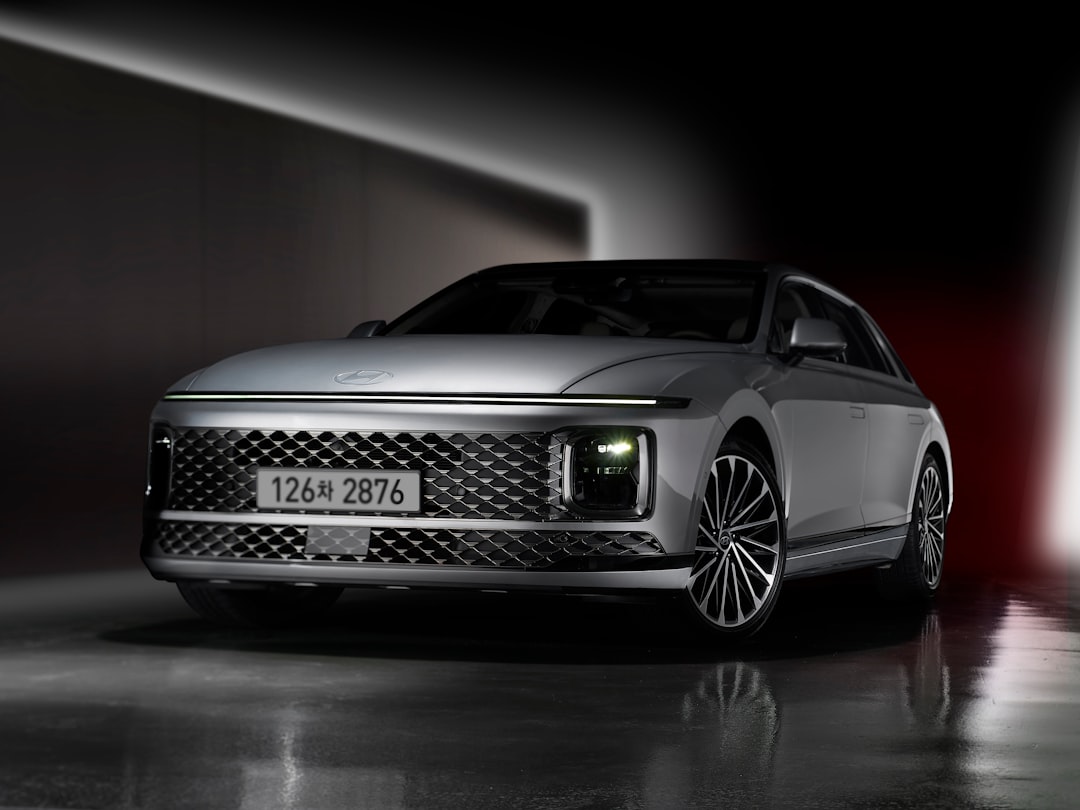
Arrival's microfactory model hinges on its use of internally developed technologies to achieve efficiency. This approach includes the use of cutting-edge elements such as robotic systems and materials like composites. These choices are aimed at making the manufacturing process more energy-efficient and reduce the impact on the environment. Furthermore, Arrival's concept of a software-controlled factory promotes adaptable production. This leads to a reduction in production delays and faster responses to changing market demands. It's a clever move, not only for streamlined production but also for maintaining competitiveness in an industry experiencing constant change. Ultimately, Arrival needs to rigorously test these technological innovations in real-world production situations if they hope to become a major player in the electric vehicle sector.
Arrival's microfactory approach in Bicester is a fascinating experiment in streamlining EV production. It centers around a novel idea of using smaller, more adaptable production units. One of the key features is the integration of both stationary and mobile robots. These robots are programmed to adapt in real-time, allowing for much faster assembly of vehicles. The hope is that this automation not only speeds things up but also reduces errors, resulting in a more consistent and efficient assembly process.
This setup uses a modular, cell-based assembly system. Instead of a traditional factory line, the production process is broken down into separate, self-contained units, each handling a specific part of the build. This setup is designed for rapid reconfiguration, potentially cutting setup times for new vehicle models down from weeks to days— a major improvement over the lengthy changeovers required in traditional plants.
Arrival's strategy involves prioritizing sourcing materials and components from suppliers within a 500-mile radius. This focus on localized supply chains not only provides a boost to the surrounding economy but also greatly simplifies the logistics of moving parts. It's an interesting approach to minimizing potential disruptions from lengthy and complex global supply chains. The benefit is twofold: it simplifies logistics and can potentially reduce production delays.
The software and data analytics that underpin the microfactory operations are quite advanced. Data from each step of the manufacturing process is fed into a system that provides real-time insights into efficiency. Engineers use this data to spot issues as they emerge and make quick adjustments to the process. They hope this will contribute to a significant increase in overall output.
The microfactory concept also integrates design and prototyping within the same space as the production lines. This streamlining of processes allows for faster iterative development of both the vehicles and the production methods themselves. This approach has the potential to shorten what could be lengthy prototype cycles from months into mere weeks.
Another intriguing element is the compact size of the microfactory. The overall footprint of Arrival's facilities is significantly smaller than a traditional auto plant, potentially just a tenth of the size. This reduced scale potentially leads to lower operational costs related to things like energy and building maintenance. Whether this will actually lead to a more economically sustainable model for future EV production is yet to be determined.
One of the core material science elements is the use of lightweight composite materials. These materials are significantly lighter than traditional steel and can offer a weight reduction of around 30%. The weight savings should lead to improved vehicle efficiency.
The microfactory design also includes in-house battery production. This strategic choice allows for closer control over battery design and integration into the vehicle chassis. This also likely contributes to weight optimization and space utilization. Furthermore, by producing the battery packs themselves, Arrival can likely refine the designs for better vehicle performance and potentially enhance safety features.
The collaboration between human workers and robotic assistants (cobots) is meant to improve both efficiency and quality control. Research suggests this human-robot interplay can lead to significant error reductions in assembly.
The flexible and modular design allows for scalable production by simply adding more production cells rather than building entirely new facilities. This modularity offers an intriguing path to expanding production without large capital expenditures and should allow production to respond more readily to changing demands.
While it's too early to declare the microfactory approach a revolution, Arrival's vision has created a fascinating and innovative approach to EV production. Its emphasis on automation, adaptability, and localized supply chains may lead to improvements in efficiency, cost, and sustainability. Only time will tell whether this approach will reshape the future of EV manufacturing on a larger scale.
Arrival's Microfactory Model Revolutionizing Electric Vehicle Production in 2024 - Arrival's US Manufacturing Pivot Aligns with Business Restructuring
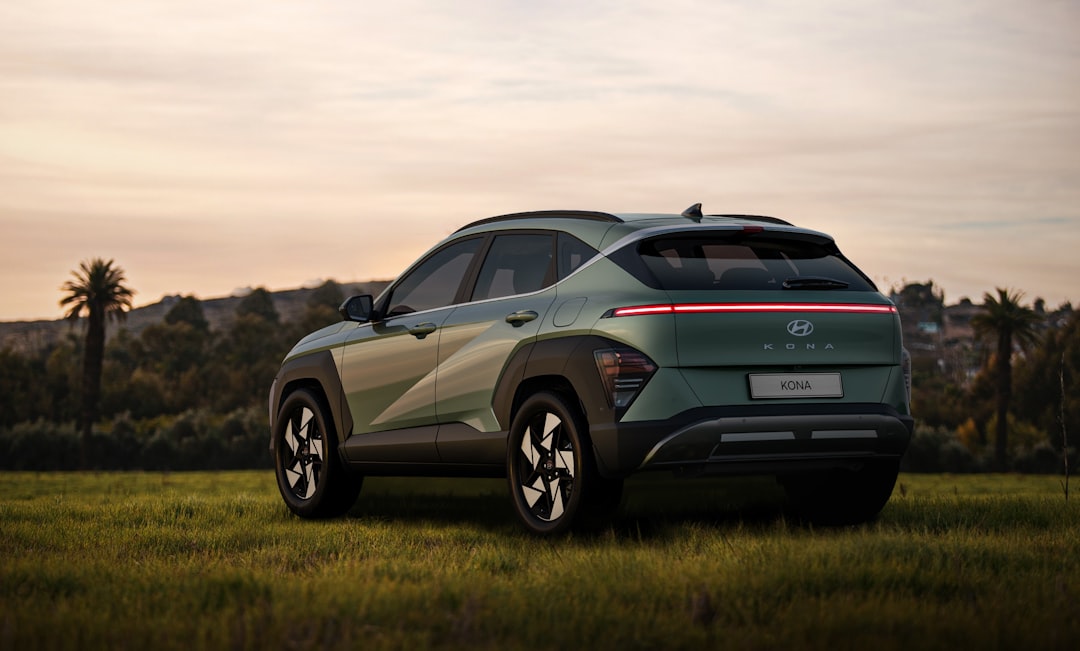
Arrival's decision to concentrate its US manufacturing efforts in Charlotte, North Carolina, signifies a major shift in strategy and is closely linked to a broader restructuring process. The company faced significant financial headwinds earlier this year, reporting substantial losses. This move, however, is also a bet on the potential of its microfactory approach. Arrival's UK microfactory has demonstrated the capacity to produce electric vans effectively, and they're hoping to replicate this success in the US market. The company's current financial position, with over $330 million in cash, gives them a degree of runway to pursue this strategy.
The US manufacturing pivot seems to be driven by broader trends in North America. Companies are increasingly looking to manufacture closer to home, driven by uncertainties in global supply chains and a desire for more regional production. However, while this trend provides opportunity, Arrival will need to adapt its operations to remain competitive. The electric vehicle sector is dynamic and is subject to evolving consumer demand and technology. Maintaining the flexibility and efficiency of their microfactory model will be vital to ensure success. It remains to be seen if their strategy can successfully deliver a consistent flow of EVs in a market that's rapidly evolving.
Arrival's recent decision to shift its focus to US manufacturing, particularly with the Charlotte microfactory, is a notable development within the evolving electric vehicle landscape. This pivot represents a departure from its initial UK-focused strategy and signals a broader restructuring effort aimed at capturing a share of the North American market.
The company's experience with the Bicester microfactory in the UK demonstrated the feasibility of producing EVs using a decentralized, modular approach. This success, coupled with a desire to capitalize on the growing demand for electric vans in the US, prompted the decision to relocate production. However, this isn't the first strategic shift Arrival has made recently, highlighting potential challenges with initial planning or a rapidly changing market.
Arrival's microfactory concept is a departure from traditional large-scale assembly lines, prioritizing flexibility and adaptability. The Charlotte facility's design, which emphasizes a modular structure, allows for expansion and adjustments as market needs evolve. The company's emphasis on localized sourcing within a 500-mile radius is interesting from a supply chain perspective, potentially offering benefits in resilience against disruptions that larger global supply chains face. This also aligns with broader trends of reshoring and a move away from reliance on China for manufacturing.
However, Arrival is not without its challenges. Financial difficulties persist, with losses reported in the first half of 2023, despite securing a bridge loan. While they currently hold a substantial cash reserve, the company’s future hinges on its ability to execute this manufacturing pivot and achieve profitability in a competitive market. The decision to prioritize certain vehicle types, like electric vans and buses, indicates an attempt to focus resources, though it introduces risks if market demands shift. The extent to which Arrival's microfactory model can achieve scalability and provide the desired degree of flexibility remains to be seen. It is an innovative concept but one with inherent risks and unknowns regarding its long-term viability.
The microfactory approach focuses on optimizing vehicle design and production processes. This includes using lightweight composite materials to reduce vehicle weight and enhance energy efficiency, a decision with implications for both performance and energy consumption. The incorporation of in-house battery production allows for a greater degree of integration and control over battery technology, potentially affecting both safety and range.
This modular design allows for greater flexibility and adaptability in response to changing market conditions. It allows independent operation of production cells, offering greater resilience to disruptions and the possibility of reduced downtime during operational issues. The software-defined nature of these facilities enables real-time monitoring and adjustment of production processes. The introduction of collaborative robots (cobots) in the assembly process aims to enhance both productivity and quality control, reducing the potential for errors.
The smaller footprint of microfactories can be advantageous regarding operational costs, possibly leading to energy savings and reduced maintenance needs. While the model holds promise, a key question revolves around its ability to scale up production to meet potential market demand, especially when compared with more traditional manufacturing approaches. The ability to adapt to rapidly evolving market preferences, such as shifting consumer demands and preferences, is crucial to Arrival's success. Whether the company can realize its vision of revolutionizing EV production through the microfactory model is a question that time and the market will answer.
Arrival's Microfactory Model Revolutionizing Electric Vehicle Production in 2024 - Microfactory Model Aims to Reduce Energy Demand and CO2 Emissions
Arrival's microfactory model seeks to lessen the energy needs and carbon footprint associated with making electric vehicles. This approach emphasizes using composite materials rather than traditional steel, leading to lighter, more energy-efficient vehicles and a reduction in manufacturing's environmental effects. This strategy aligns with a wider industry push towards more sustainable vehicle production methods, evident in the anticipated reduction in emissions linked to the production and fueling of EVs in the years to come. However, the microfactory approach is still being tested in the face of rapidly evolving electric vehicle demand. It's too soon to determine how effective this new production model will be at keeping up with the growth in electric vehicle sales and meeting the overall climate goals related to transportation. Ultimately, the long-term impact of this model remains to be seen and requires further monitoring.
Arrival's microfactory approach is built around a modular "cell-based" assembly system, where each cell focuses on a specific part of the vehicle's construction. This differs from traditional assembly lines, which often require lengthy and complex reconfigurations when switching between vehicle models. The modularity allows for quicker shifts in production, adapting to changing market demands more effectively. While this approach has potential, its ability to scale to high-volume production remains to be seen.
A key aspect is Arrival's emphasis on procuring materials locally, ideally within a 500-mile radius. This localized supply chain strategy potentially shortens the distance parts must travel, streamlining logistics. It's also intended to improve supply chain resilience by minimizing reliance on international suppliers, a factor becoming increasingly important with geopolitical shifts. This, however, could limit the range of components available or add to costs.
The modular structure supports a rapid prototyping process. Modifying vehicle designs, which might take weeks in traditional settings, can potentially happen in days at Arrival's microfactories. This fast-paced innovation cycle allows for quicker responses to market trends and the release of new vehicle configurations, but could also lead to rushed development processes.
Arrival uses advanced composite materials, resulting in an estimated 30% weight reduction in vehicles compared to conventional steel frames. This lighter weight is significant for improved vehicle efficiency and performance, particularly in electric vehicles. However, composite materials may present unique manufacturing challenges or concerns with material longevity.
Integrating battery production directly within the microfactory allows Arrival to tightly control the design and integration of the battery into the vehicle. This closer control can optimize both performance and safety features. It may be beneficial for battery technology advancement due to shorter iteration cycles, but this depends on Arrival's capability to innovate in battery production.
One of the advantages of the microfactory model is its scalability. The modular approach enables expansion by adding cells, rather than needing extensive new facility construction. This contrasts sharply with traditional factory expansions that can be very capital intensive and time-consuming. Yet, if there are critical components in the cell structure, expanding may introduce new bottlenecks.
Real-time production monitoring through integrated software provides a constant stream of feedback on production performance. Engineers use this information to quickly spot issues, such as bottlenecks or inefficiencies, optimizing the assembly process for better throughput. This constant data stream could lead to better quality control but requires the continued development and maintenance of the software systems.
Collaborative robots (cobots) are integrated to assist human workers in repetitive tasks. This human-robot partnership is intended to improve both precision and overall efficiency of the assembly process, and reduce human error, but the long term success relies on continued development and implementation of safety protocols for these complex systems.
Arrival's microfactories are designed to have a significantly smaller footprint than conventional automotive plants. This not only minimizes real estate costs but could also lead to considerable energy and maintenance savings. The lower environmental impact is also desirable. However, a smaller facility may also limit the number of products that can be produced at the same time, leading to production bottlenecks.
Arrival's pivot towards electric bus production in some of its microfactory locations indicates a responsiveness to trends in the public transportation sector. A growing interest in cleaner alternatives to traditional buses suggests there's a market for these vehicles. It's a strategic move, but depending on a singular segment in a market that is changing fast can create issues if that niche fails to grow as expected.
The microfactory model offers a potentially disruptive approach to electric vehicle manufacturing, highlighting aspects such as efficiency, adaptability, and localized sourcing. While the concept holds considerable promise, whether it can scale to meet future demand in a constantly evolving industry remains to be seen. It's a compelling example of the creative solutions being explored to address the challenges of electric vehicle production.
More Posts from agustin-otegui.com: